We are standing in Glashütte in front of a mileage post from 1734 next to the A. Lange & Söhne manufacture, which signals the distances to the surrounding villages and towns. Back then, the post indicates, it took six hours and fifteen minutes to get from Glashütte to Dresden by horse-drawn carriage. Glashütte was nothing more than a sleepy little town, despite once playing a not insignificant economic role in the region due to silver ore mining. Generally, however, cultural and social life remained centred in Dresden, the state of Saxony’s royal seat.
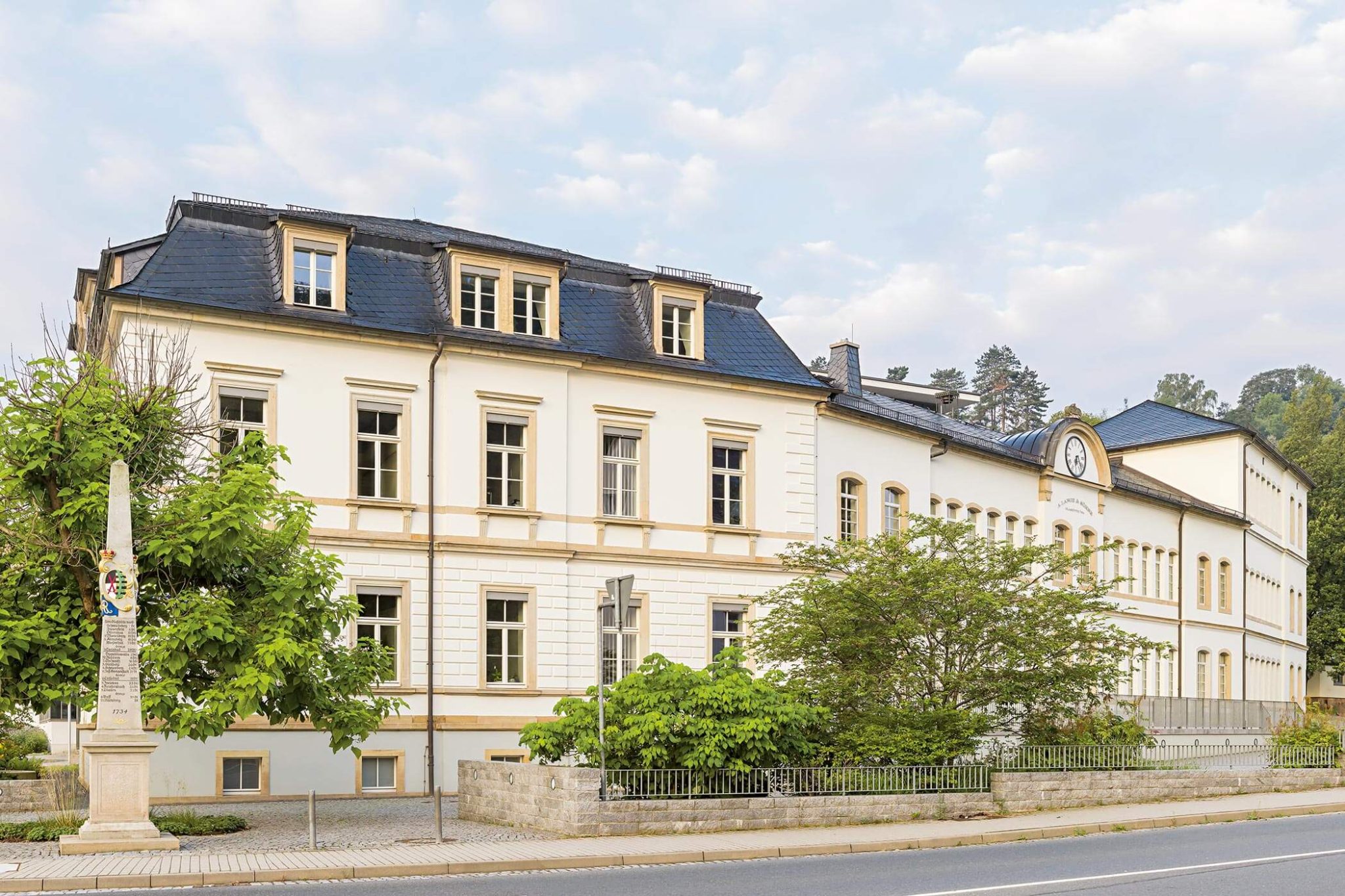
When we look around Glashütte today, there is no sign of the sleepy village idyll of the past. There are manufacturing and administrative buildings all around us, although they don’t look industrial, but rather blend charmingly into the landscape. The majority are watch companies: today, Glashütte is known across the world for its production of watches ‘Made in Germany’.
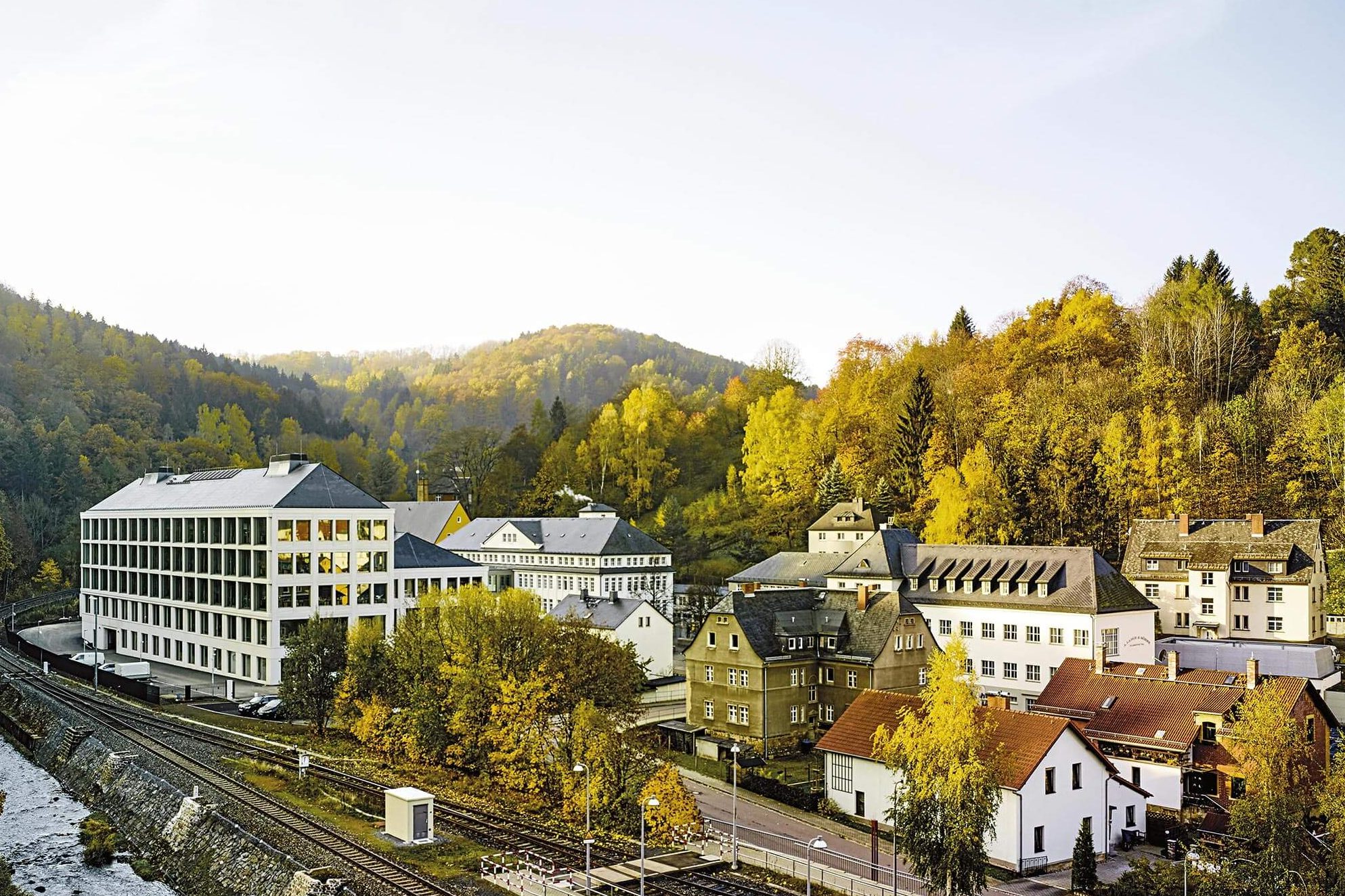
The reason for our trip to Glashütte is owed to a visit of the very watch manufacture that laid the foundations for watchmaking in Saxony. It was Ferdinand Adolph Lange, founder of the eponymous watch manufacture A. Lange & Söhne, who brought watchmaking to Glashütte in the middle of the 19th century. We have come to peer over the shoulders of the very watchmakers responsible for the timepieces that are oft-regarded as the holy grail amongst collectors. Our aim is to learn about the history and evolution of the timepieces since the manufacture was re-established almost 35 years ago – in particular the Zeitwerk, whose design is a tribute to an important event in the life of Ferdinand Adolph Lange. But first, you have to ask yourself why founder Lange chose the remote town of Glashütte, six hours and fifteen minutes away from Dresden, as the location for his life’s work in the first place.
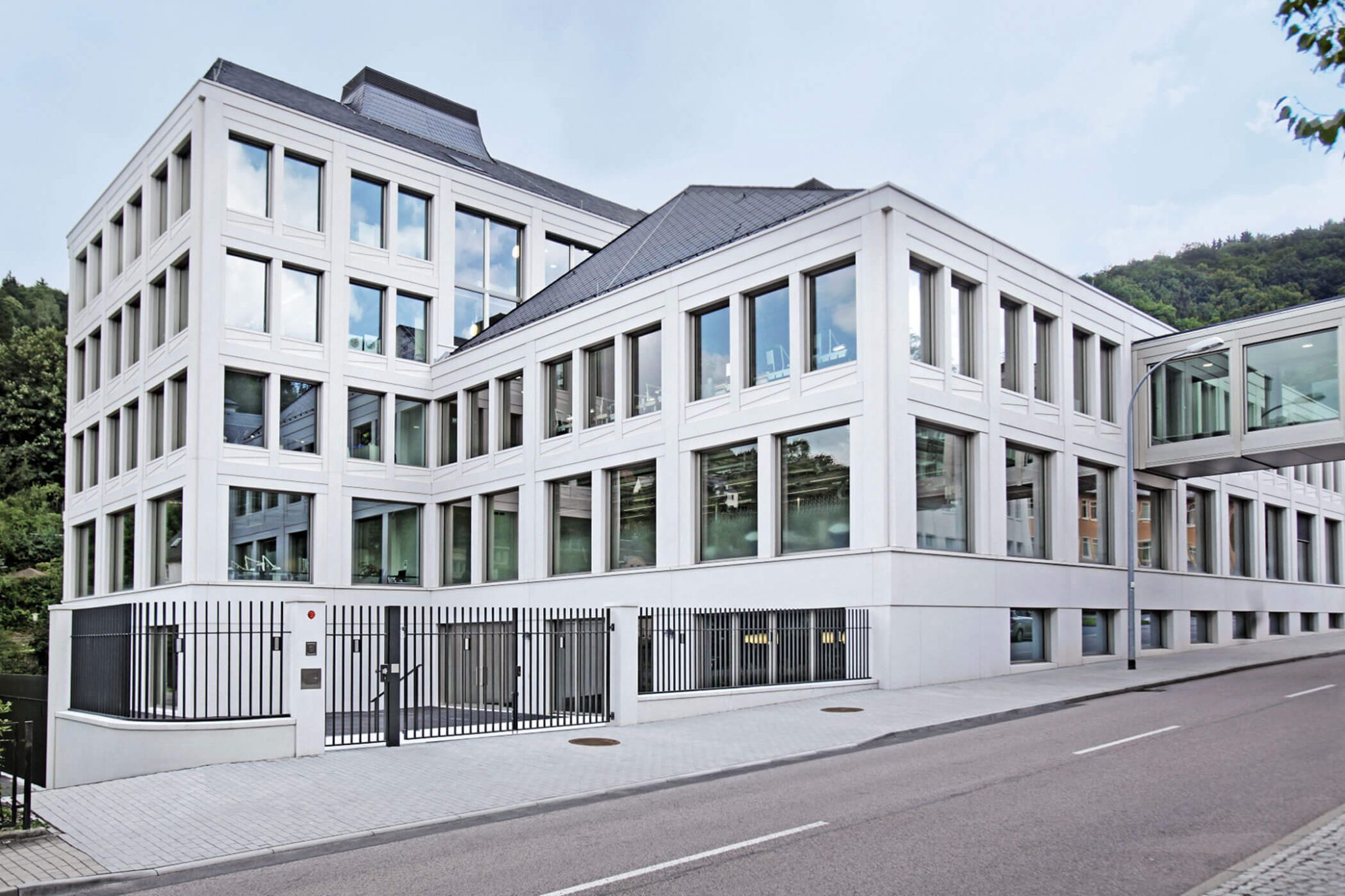
Following in the footsteps of Breguet
Before Ferdinand Adolph Lange came to Glashütte, he began his watchmaking career in Dresden, where between 1830 and 1835, he served as the apprentice to master watchmaker and court mechanic Johann Christian Friedrich Gutkaes alongside his school education. After completing his apprenticeship with honours, Lange remained with Gutkaes working as an assistant until 1837.
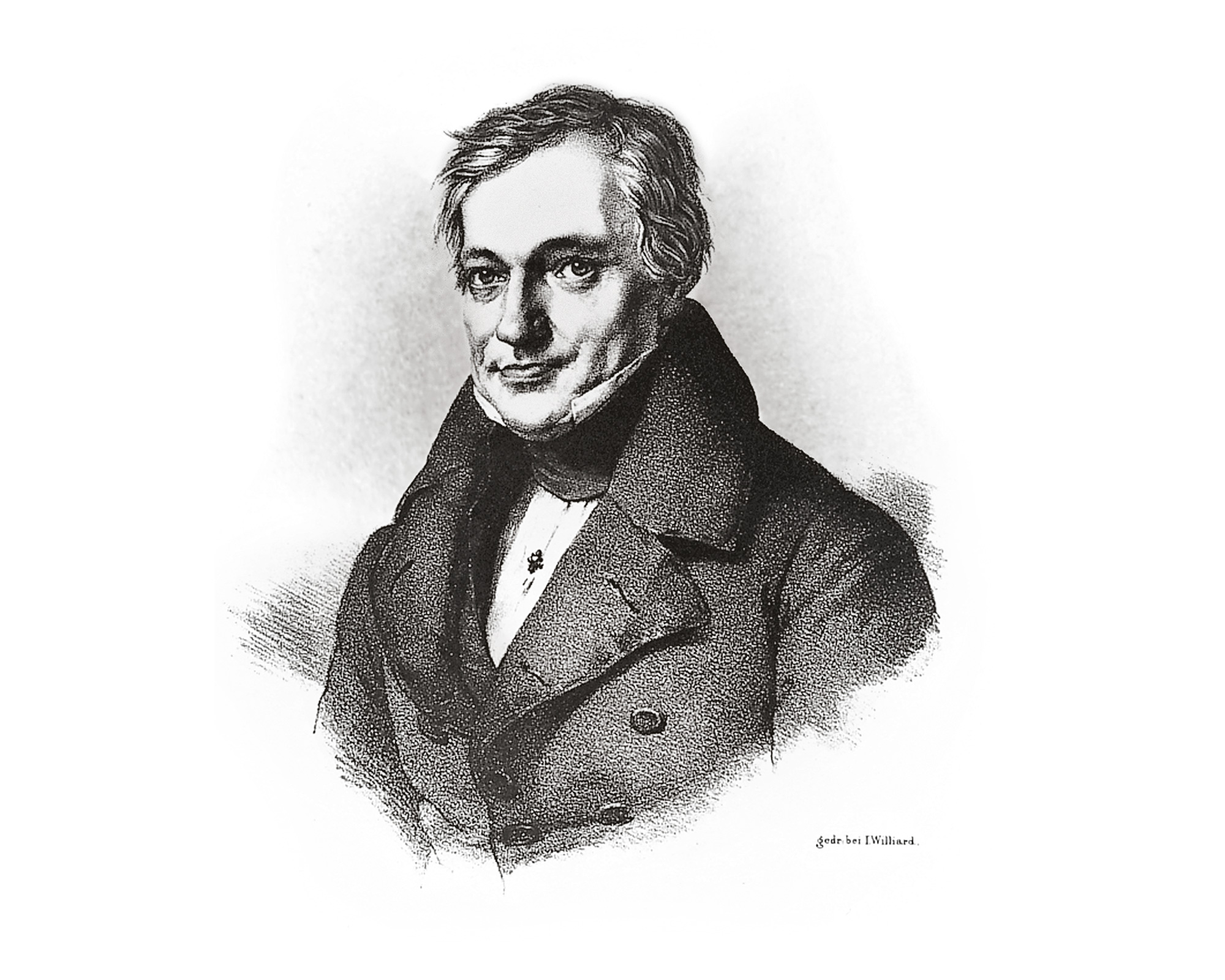
Johann Christian Friedrich Gutkaes
Ferdinand Adolph Lange showed much promise as a craftsman and left a lasting impression on Gutkaes – but eventually, it was time for him to move on. In 1837, he travelled to France and joined the Austrian watchmaker Joseph Thaddäus Winnerl (1799-1886), a former pupil of Abraham-Louis Breguet. Lange was soon promoted to workshop manager there, and as if that wasn’t enough for a man in his early 20s, Lange also studied astronomy and physics at the Sorbonne University in Paris. It was during this time that he wrote his sketch and travel notebook, which impressively demonstrates the dedication with which Lange was involved in watchmaking at the time. It contains tables, construction drawings, mechanisms and his own calculations, in which he converted the Parisian rule, which was common at the time, into the modern metric system.
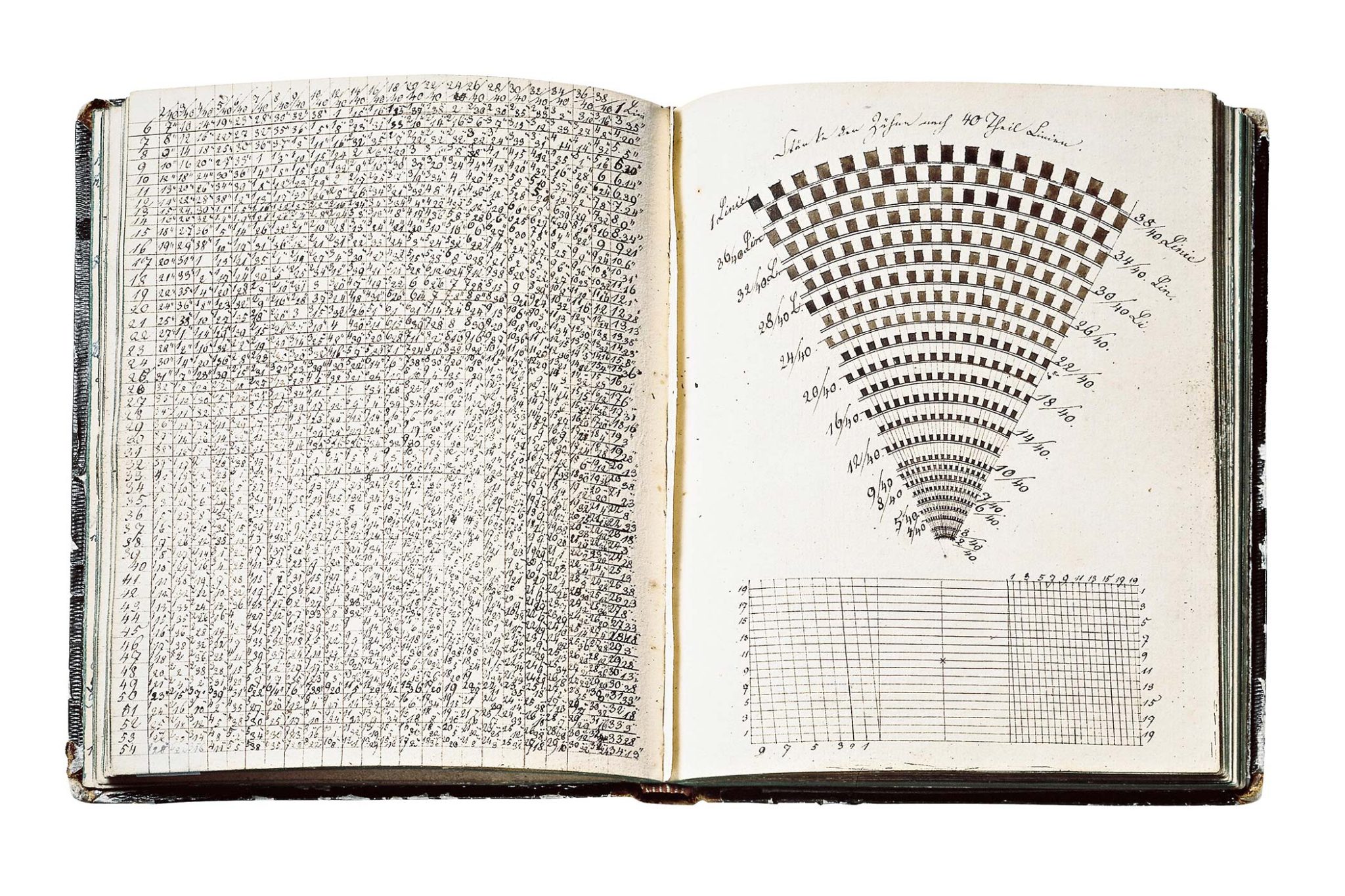
Ferdinand Adolph Lange’s sketch and travel notebook
After four years, Ferdinand Adolph Lange returned to Dresden, passed his master craftsman’s examination, joined the business of his former supervisor Gutkaes, and married his daughter Antonia.
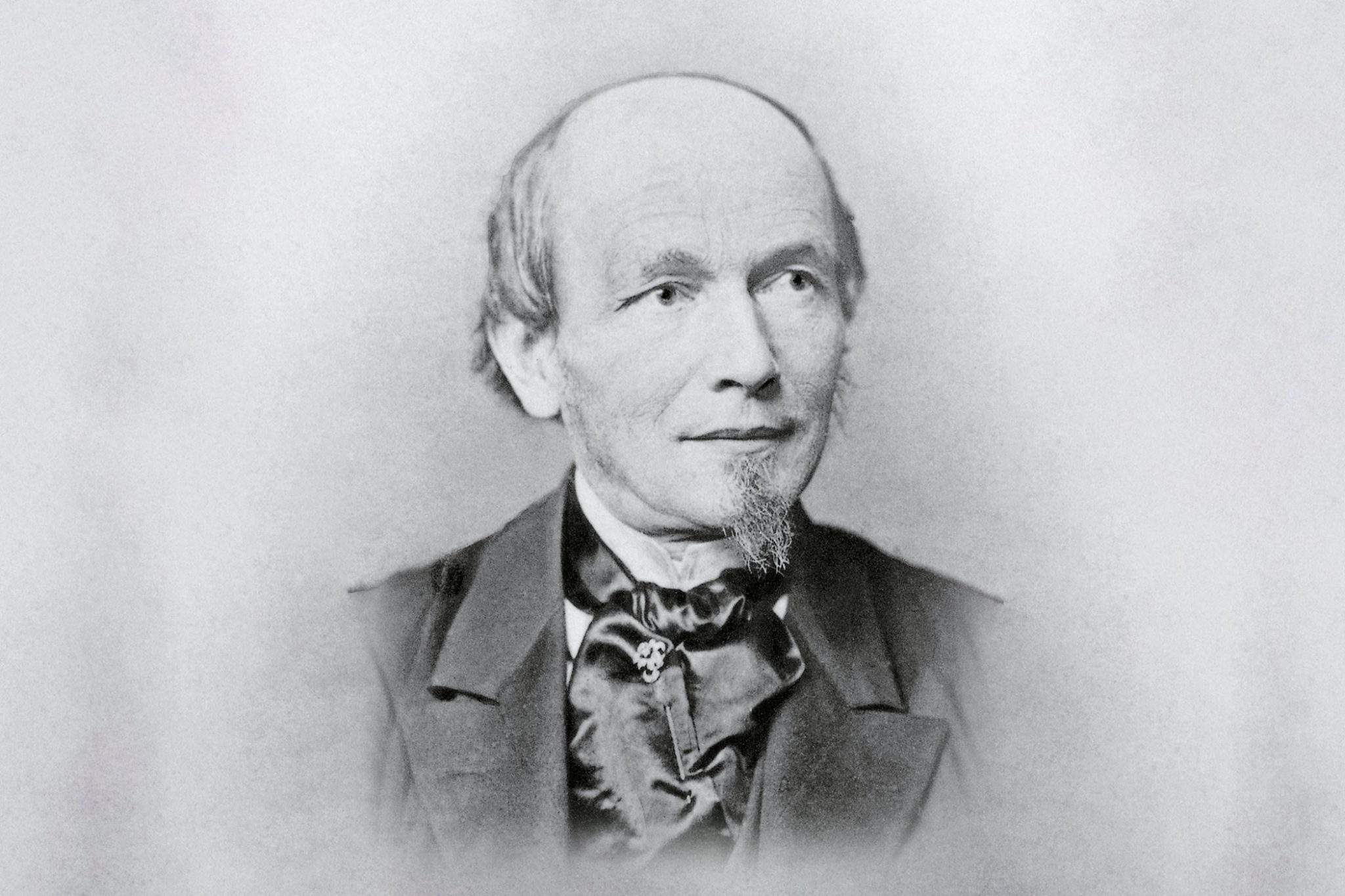
Ferdinand Adolph Lange
In 1838, Gutkaes received a commission from the king to build the stage clock for the opera house in Dresden, designed by architect Gottfried Semper. The large clock in the auditorium was to be built so that the audience would not have to constantly take out their pocket watches and sound chimes in the dark auditorium during the theatre performance. Gutkaes designed and built the clock in his workshop, where Ferdinand Adolph Lange also lent a hand. The challenge was to build a clock that could be easily read from every seat in the theatre. The result was the Semper Opera’s famous 5-minute clock, which can still be seen there today. The special thing about it was that it showed the time using a digital display (without a dial and hands), as this made it easier to read the time from a greater distance. The construction became the inspiration for the design of the Lange outsize date and later also for the digital display of the Zeitwerk watch models from A. Lange & Söhne.
Lange may not have been as inventive as Breguet, Harrison or Mudge, but he had the entrepreneurial ambition to establish watchmaking in Germany, organised according to the manufactory system and based on scientific knowledge. He is rightly regarded as the founder of Saxon precision watchmaking. Almost all the watch brands still based in Glashütte today can ultimately be traced back to Lange; some watchmakers learnt their trade at Lange and then set up their own brand.
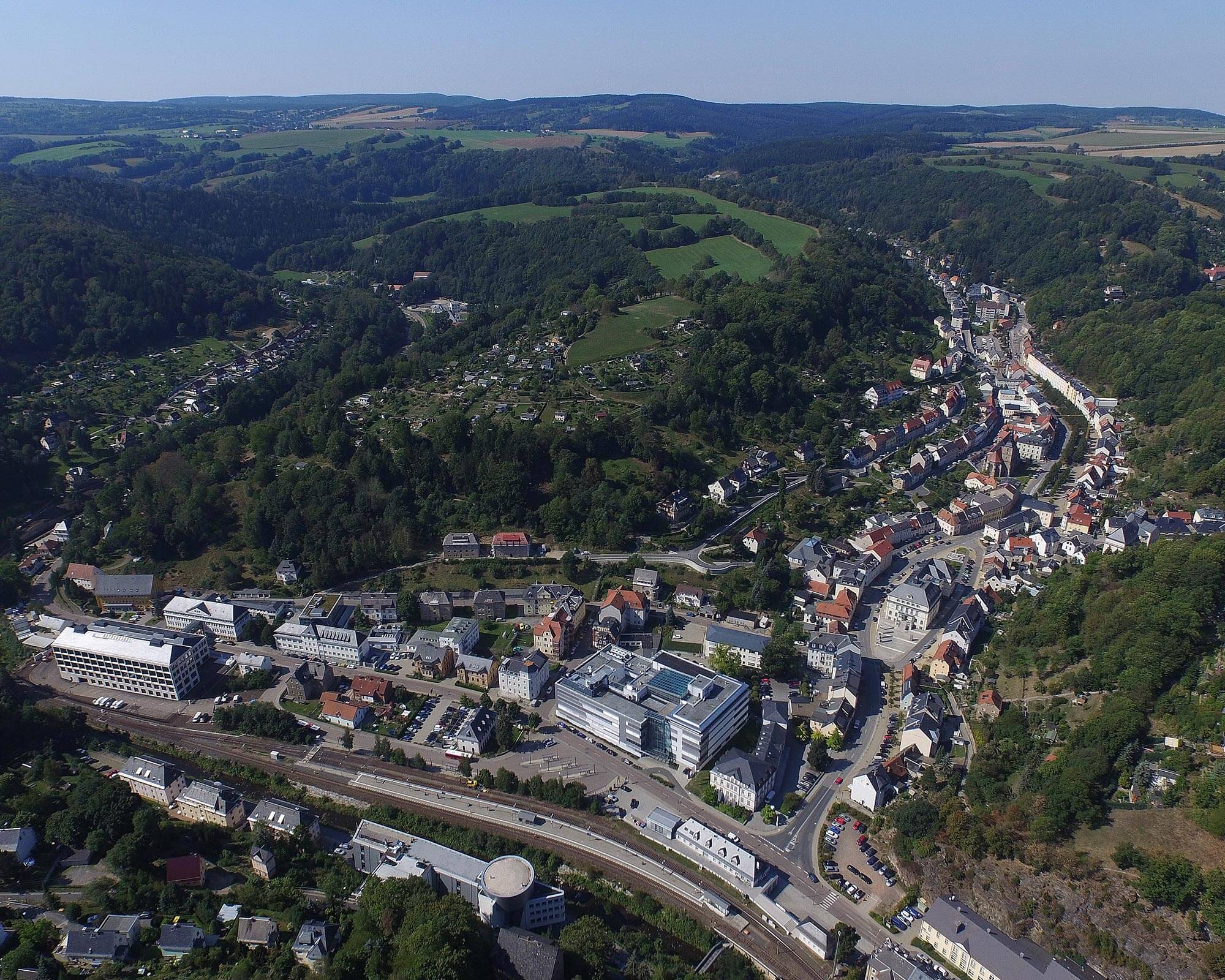
Glashütte
Lange’s workshop in Glashütte
But why Glashütte? Well, in this rural region, inhabitants were skilled in many trades. Although they had nothing to do with watchmaking, much of the populace were talented craftsmen, to whom Ferdinand Adolph Lange could bring the necessary knowledge. He was determined to set up his workshop in Glashütte and bring new work to the impoverished region. At the beginning of the 19th century, the ore reserves had been largely depleted and the economic situation in the region was deteriorating. Lange drew up a rough business plan and approached the Saxon government. After countless letters and a great deal of persuasion, in 1845, the relevant ministry approved a repayable loan of 5,580 thalers for the employment and training of 15 watchmaking apprentices in Glashütte, and a further 1,120 thalers for the purchase of tools. On 7 December 1845, Ferdinand Adolph Lange welcomed his first apprentices to Glashütte. This also marked the birth of the watch manufacture A. Lange & Cie, as it was called at the time. It was not until 1868, after his son Richard joined the company, that the name was changed to A. Lange & Söhne.
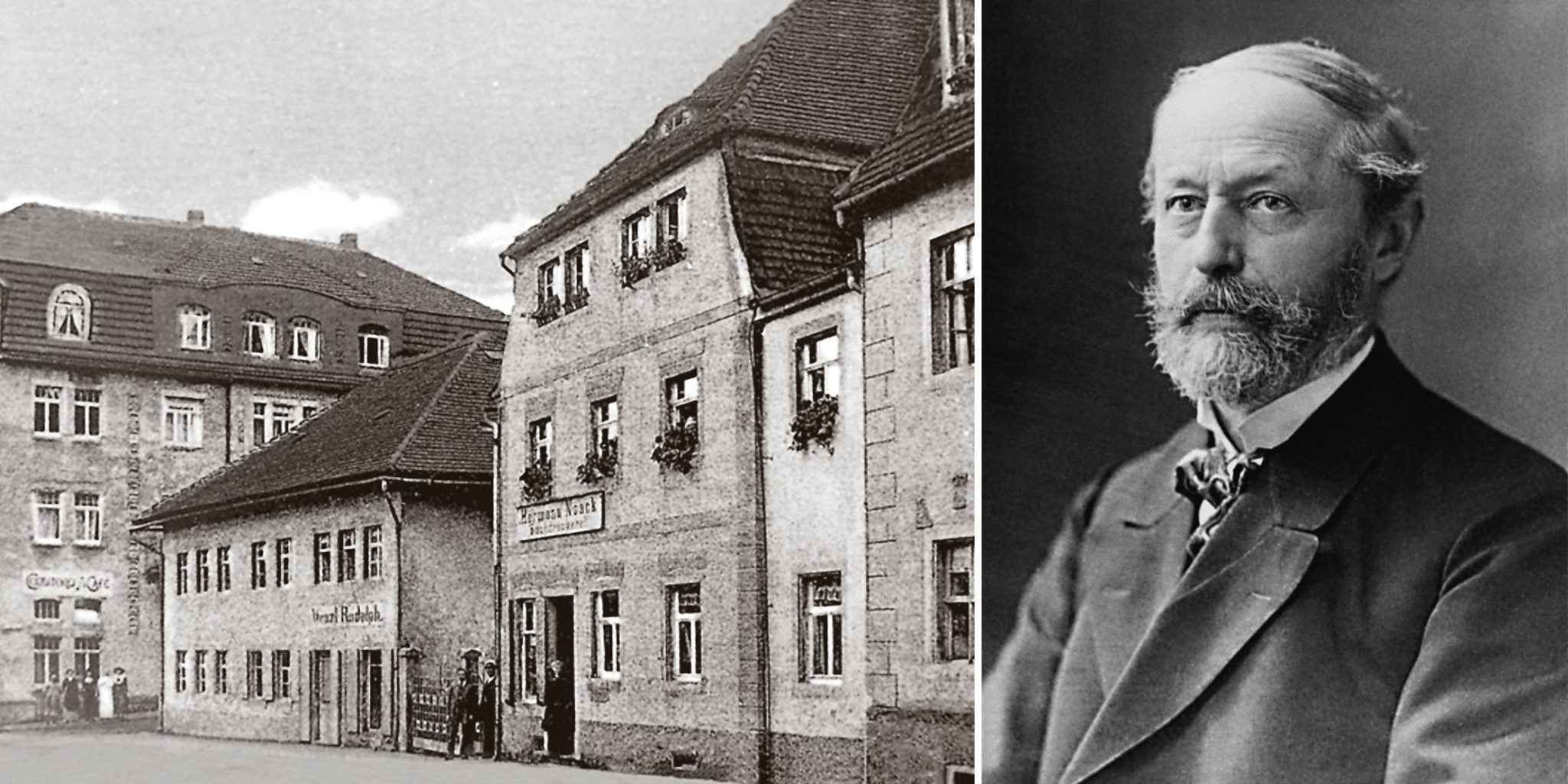
The modern foundation of A. Lange & Söhne
We are now going to take a leap in time, as anything else would go beyond the scope of this article. After all, our visit to the A. Lange & Söhne manufacture is owed to examining the various stages in the production of contemporary Lange timepieces. But first, let’s take a minor step back in time: after the A. Lange & Söhne brand fell victim to expropriation in the Soviet occupation zone in 1948, it took until 1990 for the family business to be revived. Walter Lange, great-grandson of founder Ferdinand Adolph Lange, and his companion, manager Günter Blümlein, carried the company into a new era in 1990 with the re-establishment of the Lange manufacture. “We had no watches that we could build and sell, we had no employees, no buildings and no machines,” Walter Lange later recalled. “But we had a vision of the best watches in the world, and we wanted to manufacture them in Glashütte once more.”
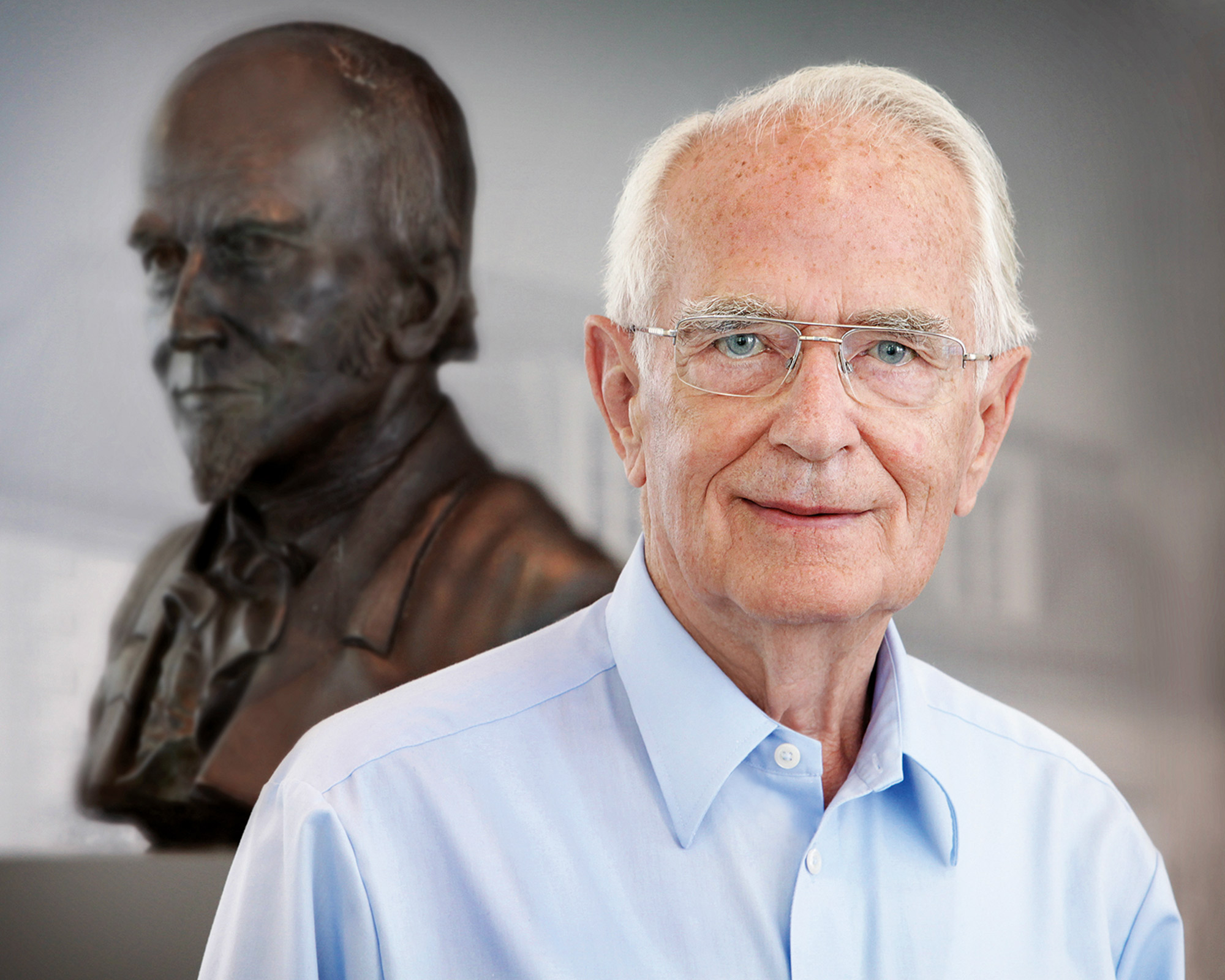
Walter Lange, great-grandson of founder Ferdinand Adolph Lange
In 1994, Walter Lange and Günter Blümlein presented the first collection of the modern era with the Lange 1, the Saxonia, the Arkade and the ‘Pour le Mérite’ tourbillon. The Lange 1, with its large date and decentralised time display, became the main protagonist. The pair also established craftsmanship and design elements in their wristwatches that were inspired by the watch manufacture’s historic pocket watches, soon becoming unmistakable quality features of Lange timepieces. These include the hand-engraved balance cock, the swan-neck fine adjustment, the three-quarter plate – developed by Ferdinand Adolph Lange in 1864 to improve the stability of the movement – blued screws, and the chain and fusée drive as first seen in the ‘Pour le Mérite’ tourbillon from 1994. The power reserve indicator has also become a typical feature of Lange wristwatches and, with its ‘UP/DOWN’ marking, is inspired by classic pocket watches created by Ferdinand Adolph Lange.
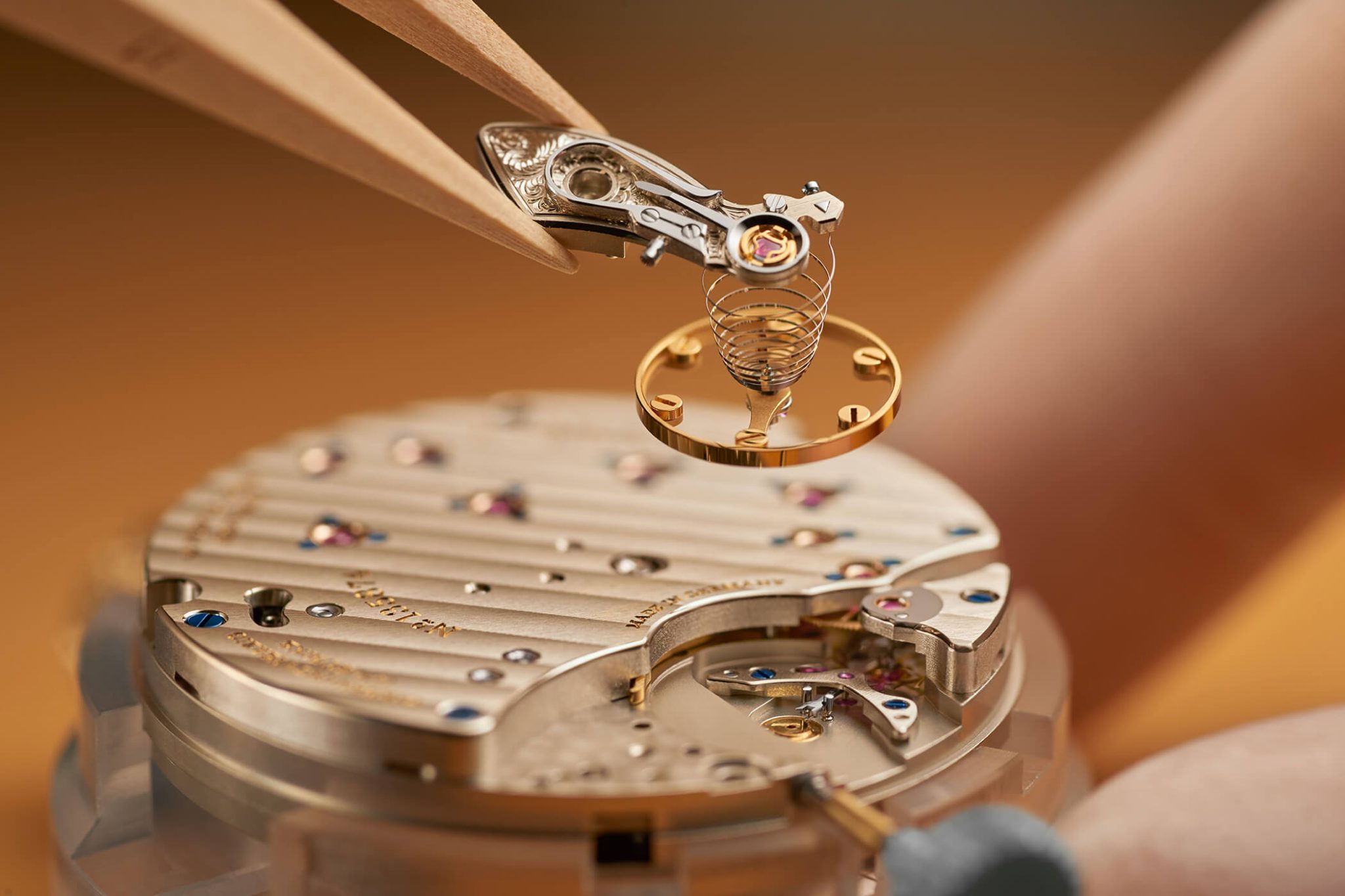
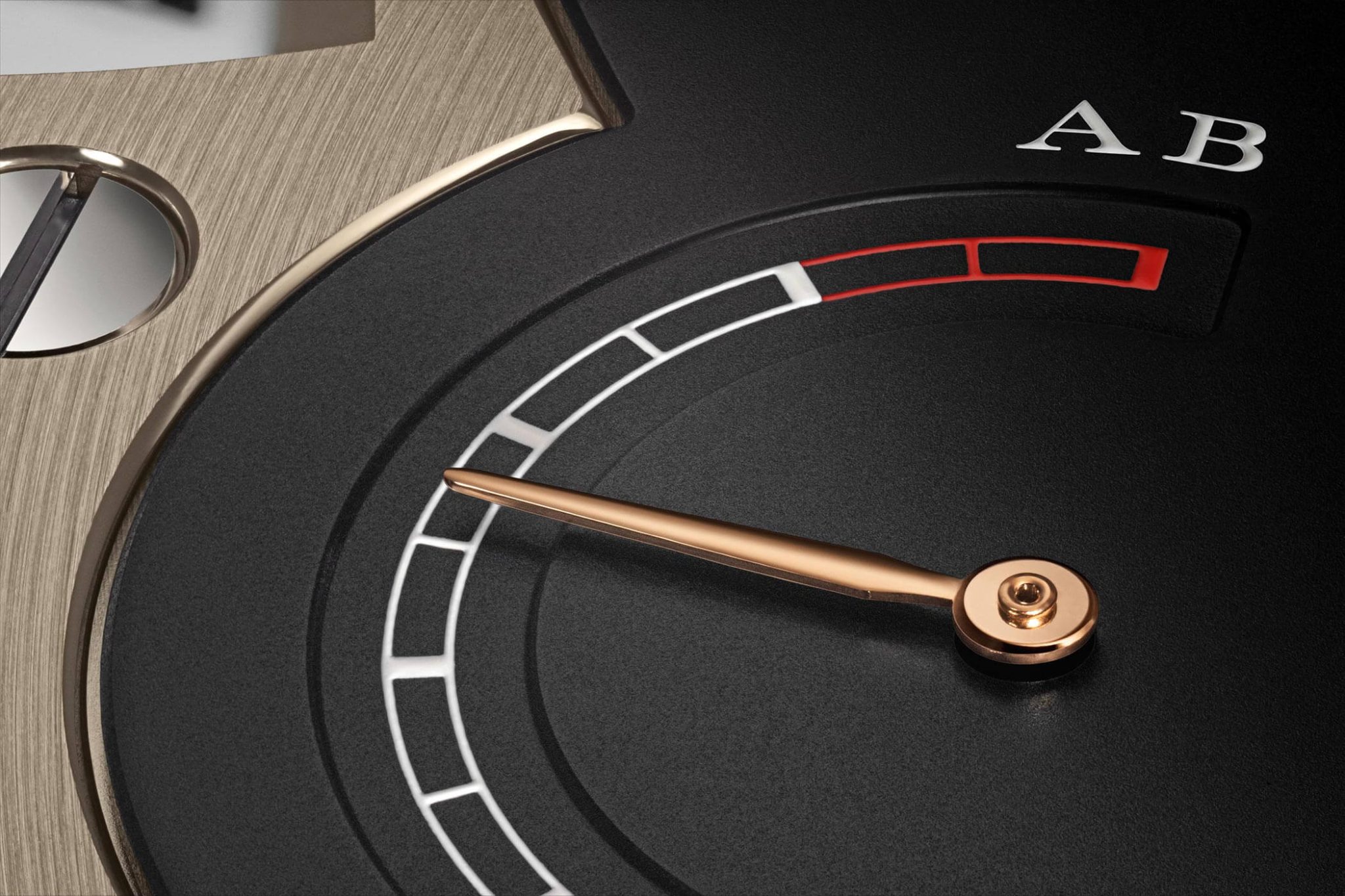
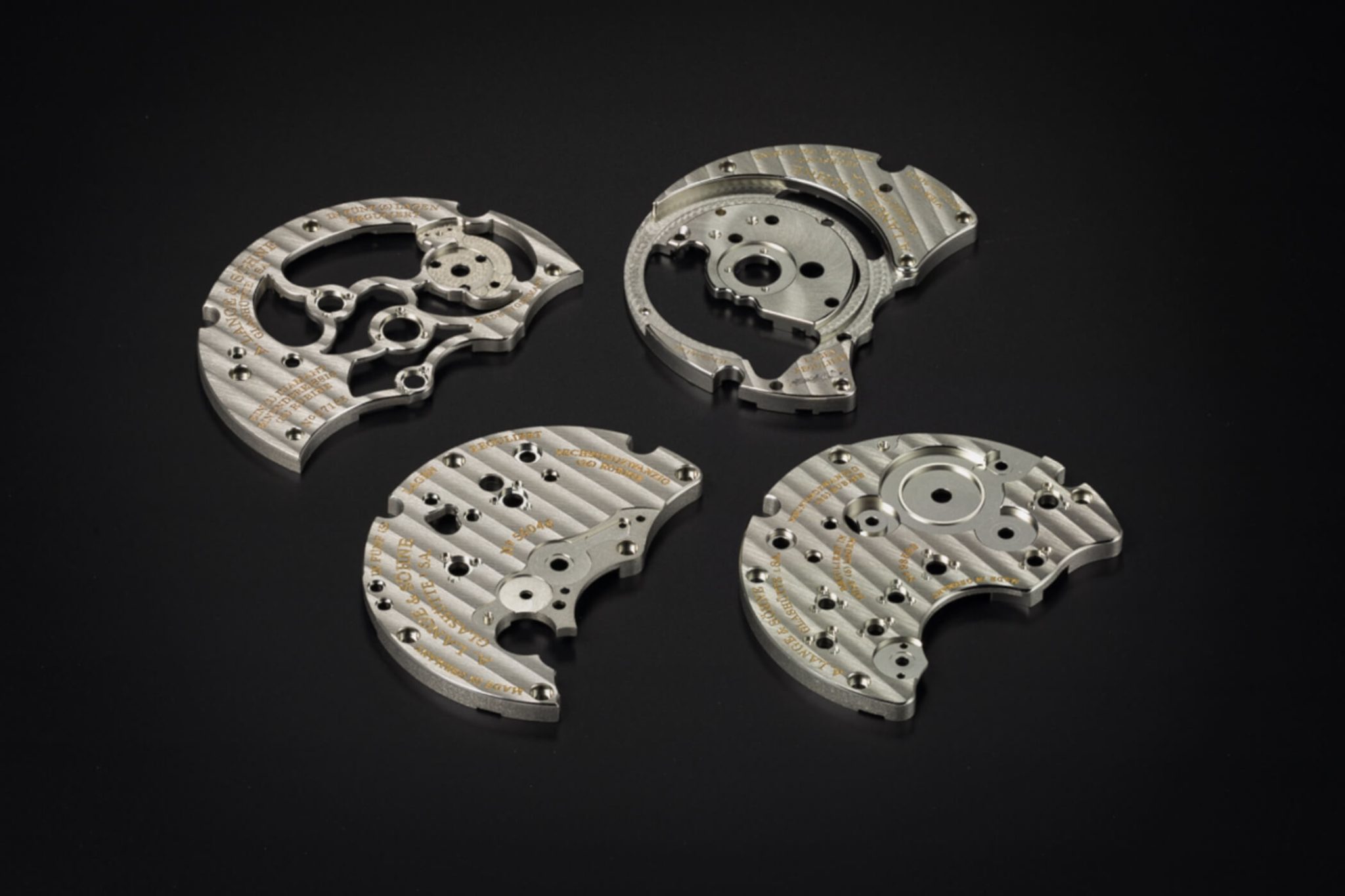
71 new movements in 33 years
For many collectors, a Lange watch represents the pinnacle of their collection. This is because the dedication and precision with which the watchmakers produce the elaborate movements is reflected in the aesthetics of the watches. Almost all parts of the movement are produced in the manufacture, and this even includes the balance spring since 2003. As the supreme discipline of movement component production, only a few watch brands worldwide have mastered production of the balance spring.
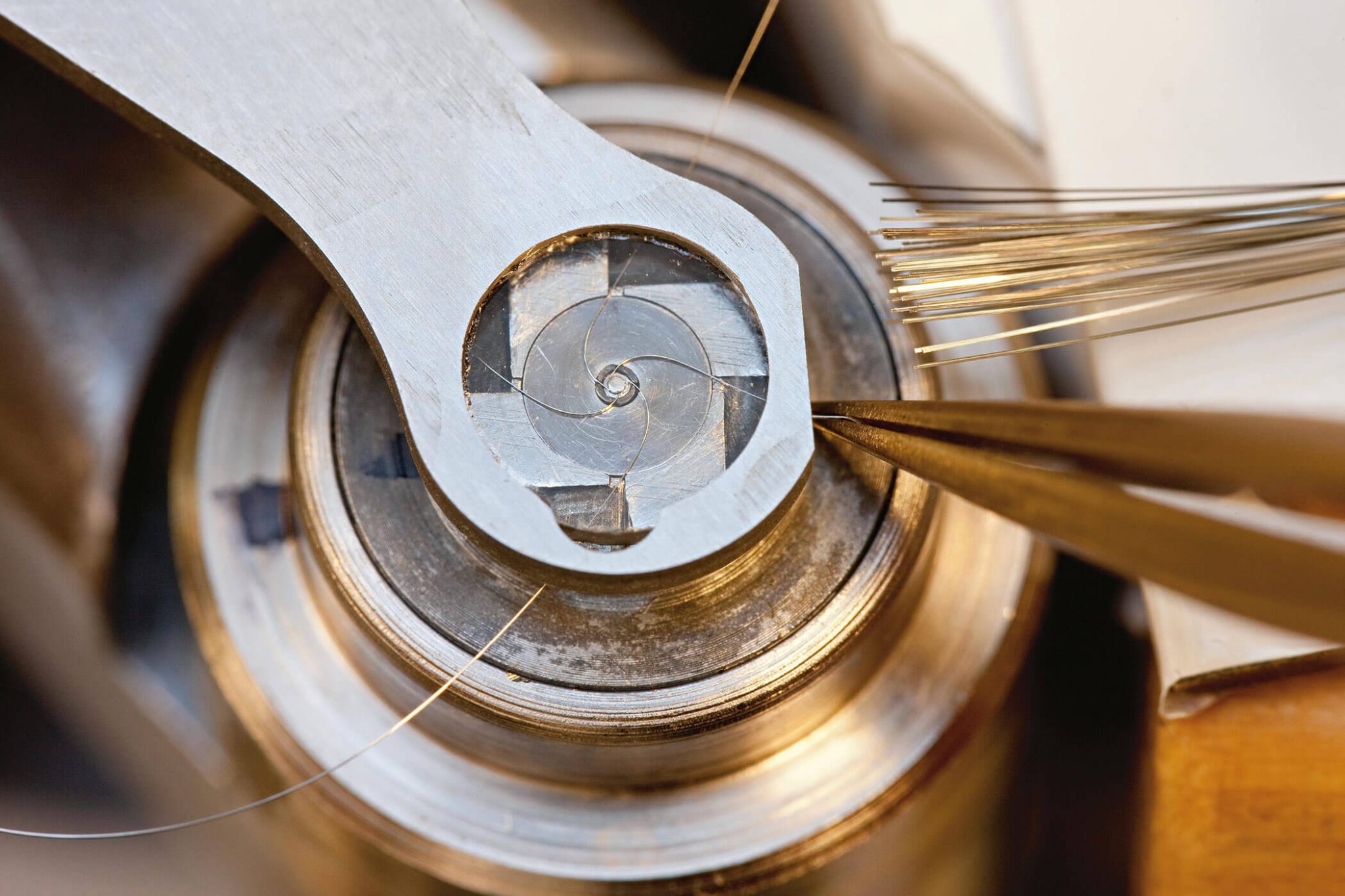
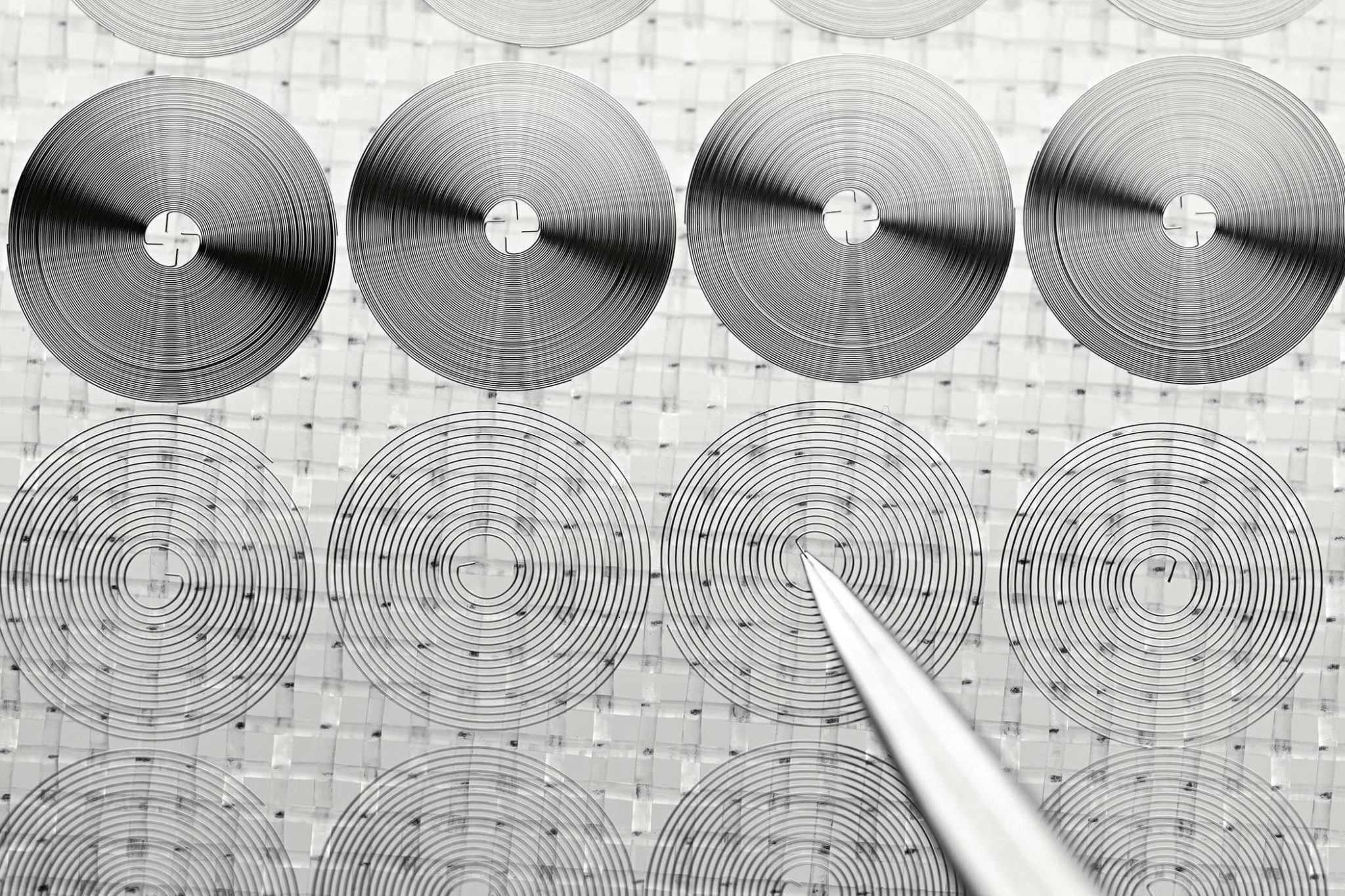
All movements are designed and produced at the A. Lange & Söhne manufacture in Glashütte. There have now been 71 new calibres since the company was founded in 1990, which means an average of around two new calibres per year. This is a more than respectable feat, especially when you consider the complexity of the watches. First and foremost, there’s the Grand Complication from 2013, which has a striking mechanism with large and small chimes, a minute repeater, a perpetual calendar, and a rattrapante chronograph with split seconds. There’s also the ingenious and patented mainspring barrel construction with rewinding mechanism that can be found in the latest generation of timepieces, in which Lange’s designers have managed to increase the power reserve from 36 to 72 hours without enlarging the movement. Or there’s the Triple Split, the world’s first mechanical rattrapante chronograph, which masters comparative time measurements over several hours to an accuracy of one-sixth of a second.
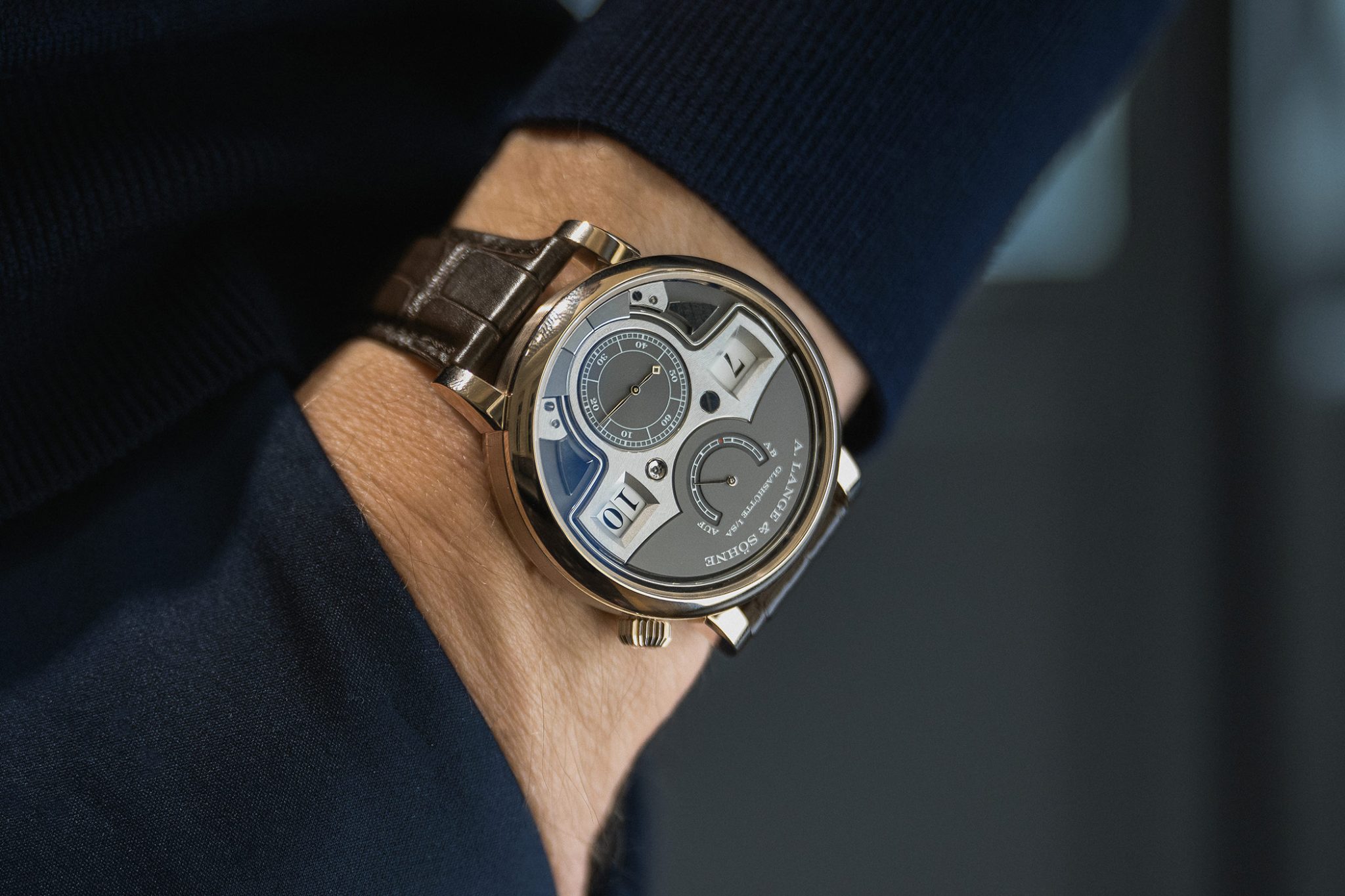
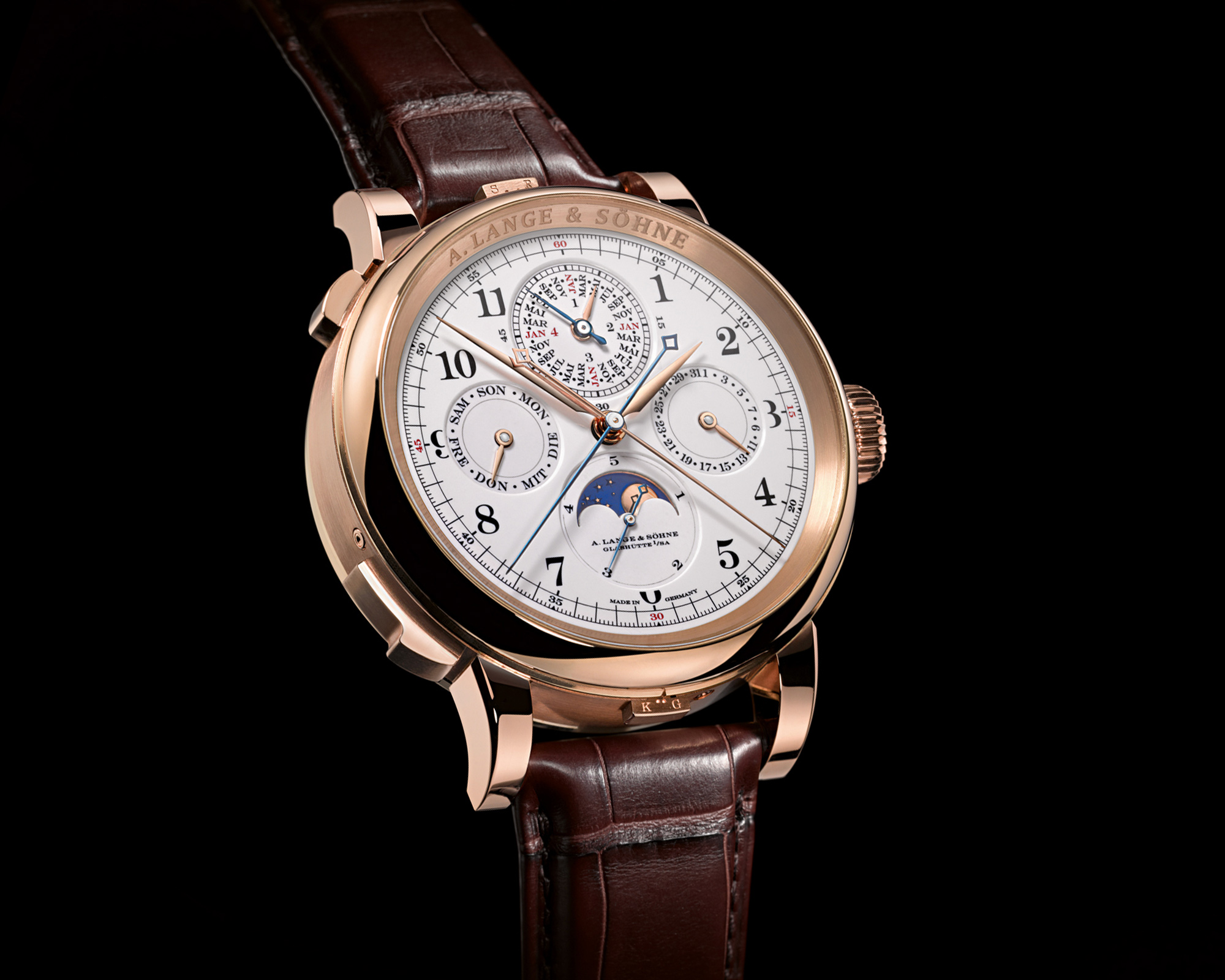
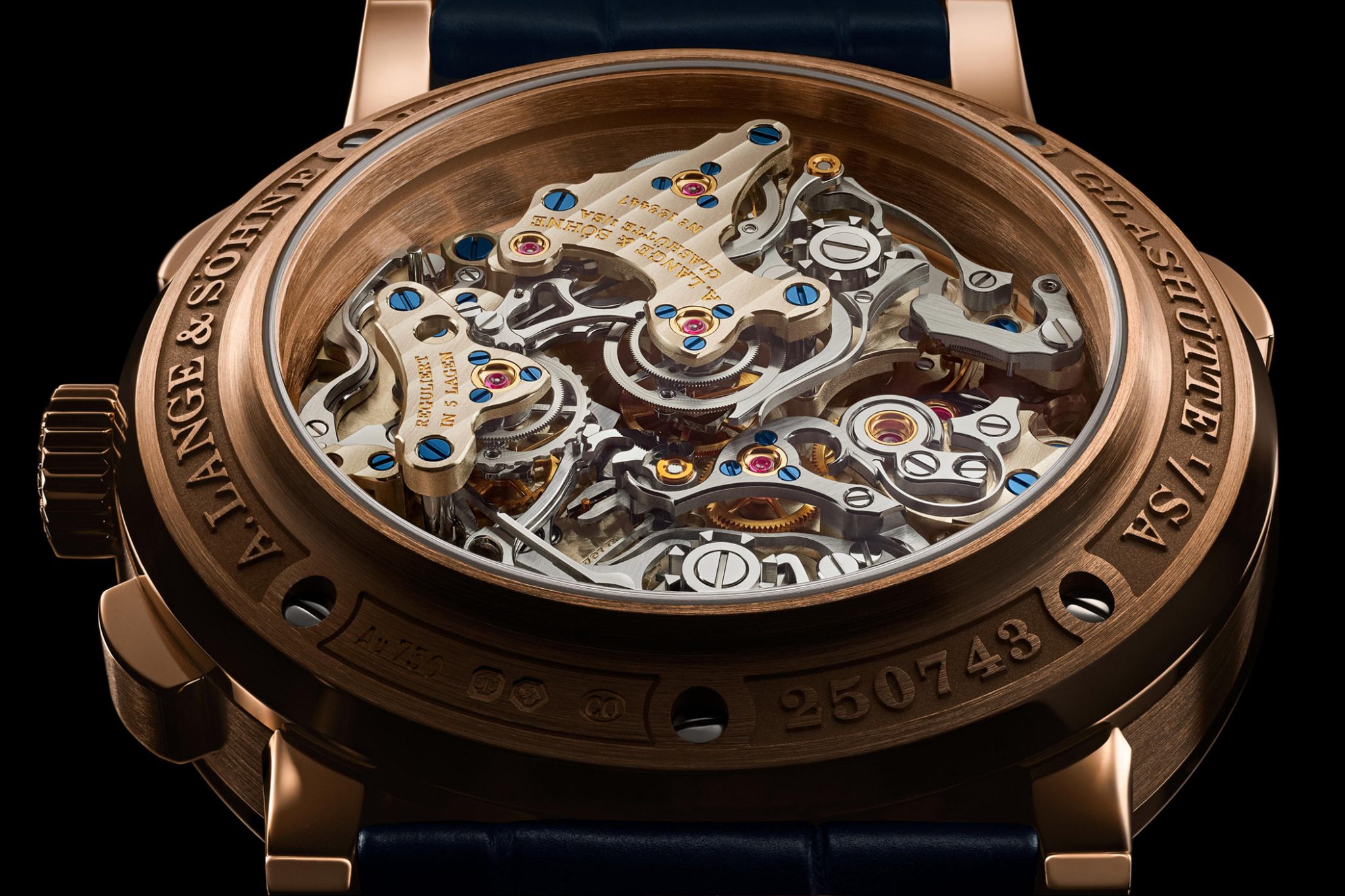
The list could go on, but another equally important point is the level of depth that goes into the movement decoration. The craft of decoration is extremely highly valued at the manufacture, transforming the watches into real horological works of art. Not only the visible parts are bevelled, polished and engraved, but also the components that lie inside. A special feature of Lange watches is the balance cock, which is also engraved by hand with a floral pattern typical of Lange. Each engraver leaves his own personal signature during the finishing process, making each piece unique.
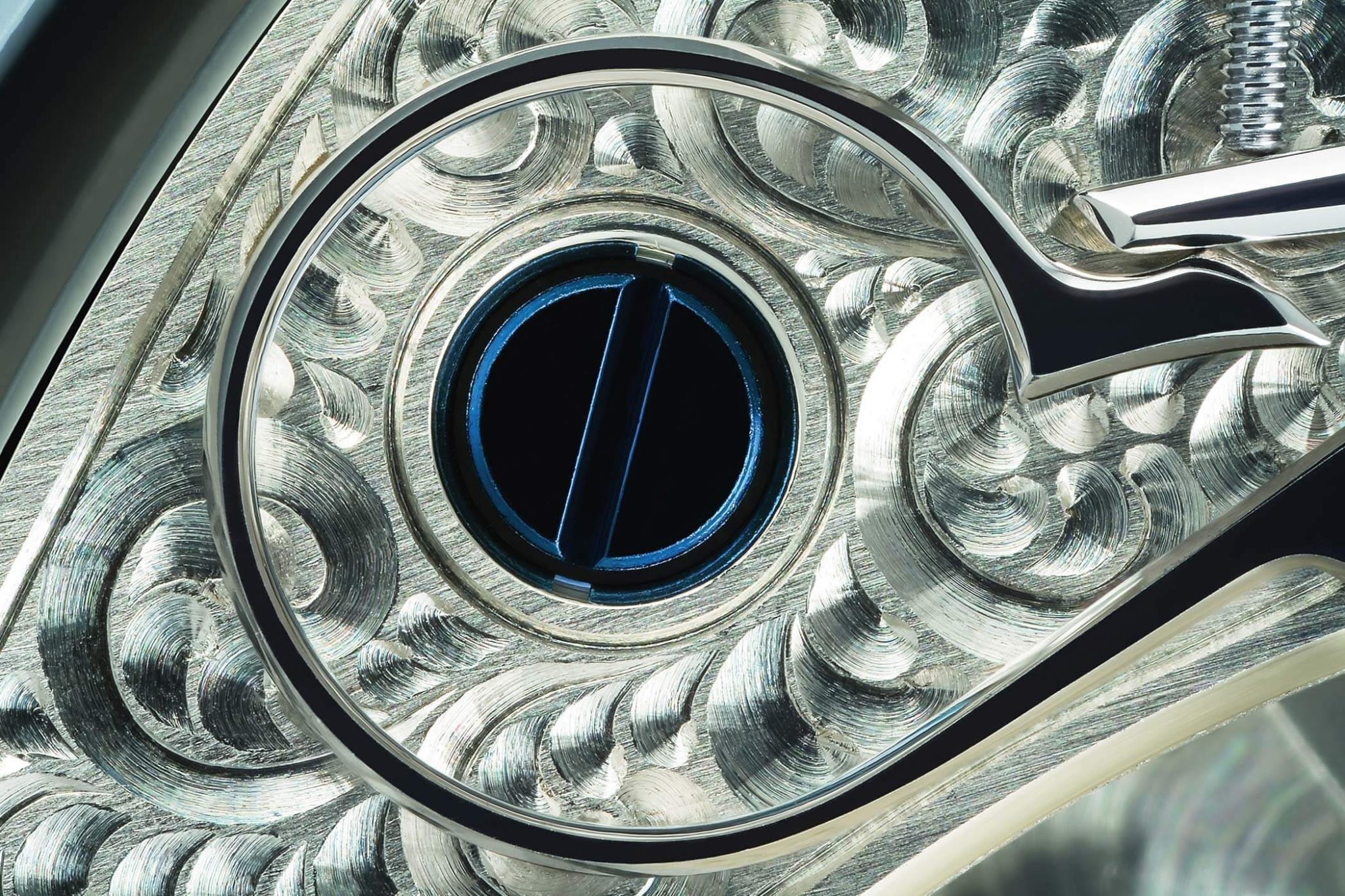
Other hallmark Lange finishes include the Glashütte bracelet polish, sunburst polish, linear finish, circular grain, mirror polish, bevel polish, flat polish, black polish, perlage, anglage and the polishing of inner corners. Relief engraving and enamelling techniques are also used in Lange’s ‘Handwerkkunst’ (German for craftsmanship) editions. Another maxim that is unique to Lange is double assembly, in which each movement is completely dismantled after initial assembly and adjustment and, after some parts have been given the finishing touches, finally assembled with new blued screws.
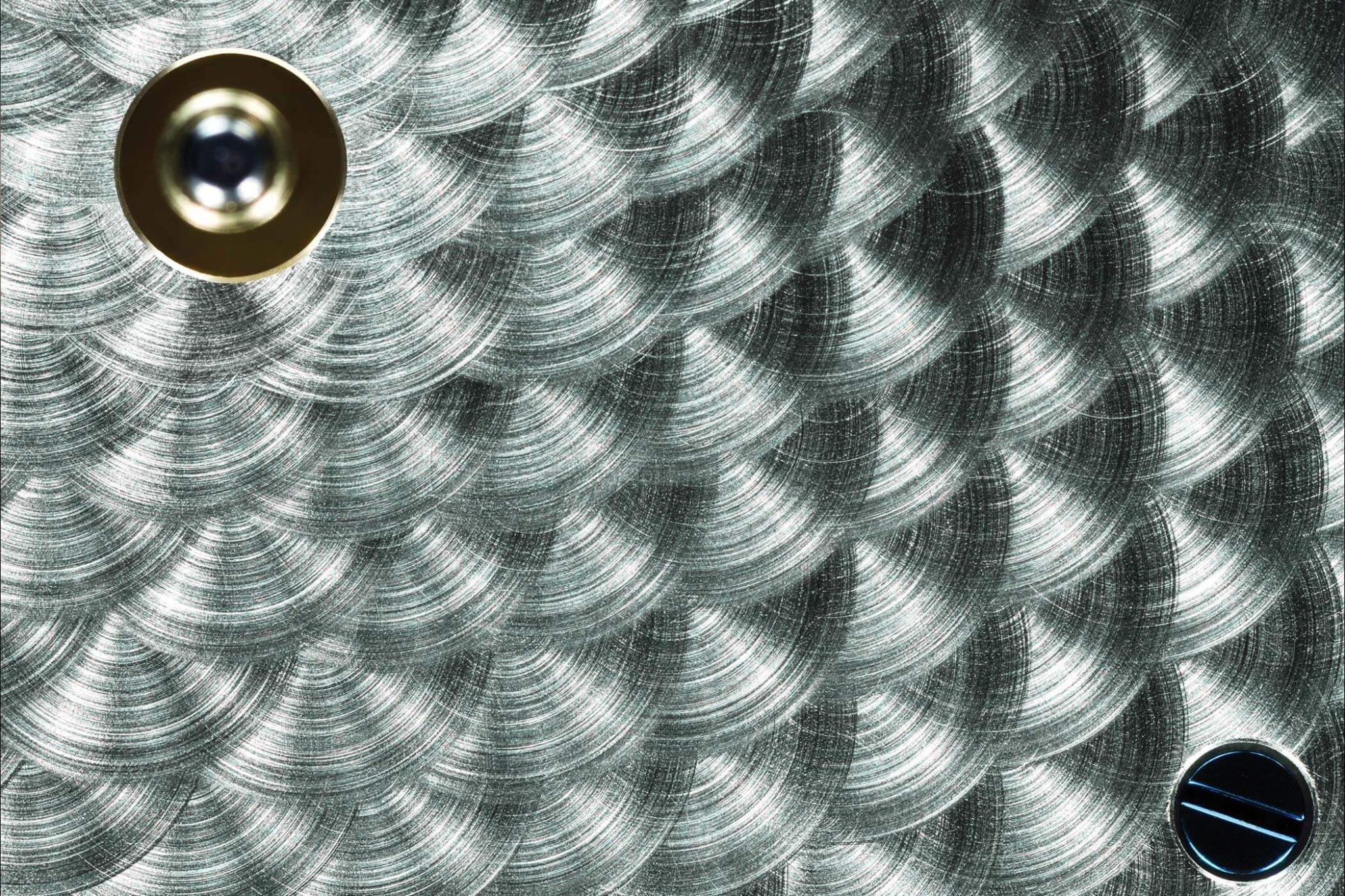
The splendour and fascination of these timepieces for their owners lies not only in the depth of production and their aesthetic appearance, but also in the fact that all creative processes, as well as development, production, decoration and (double) assembly, still take place in Glashütte today. Today, A. Lange & Söhne has four main production and administration buildings: the parent company, which was bought back in 2000, the Lange I, Lange IA and Lange II production facilities, and a new manufacture building inaugurated in 2015. It is here, at the latter location, that we stand in today, preparing to take a detailed look behind the scenes.
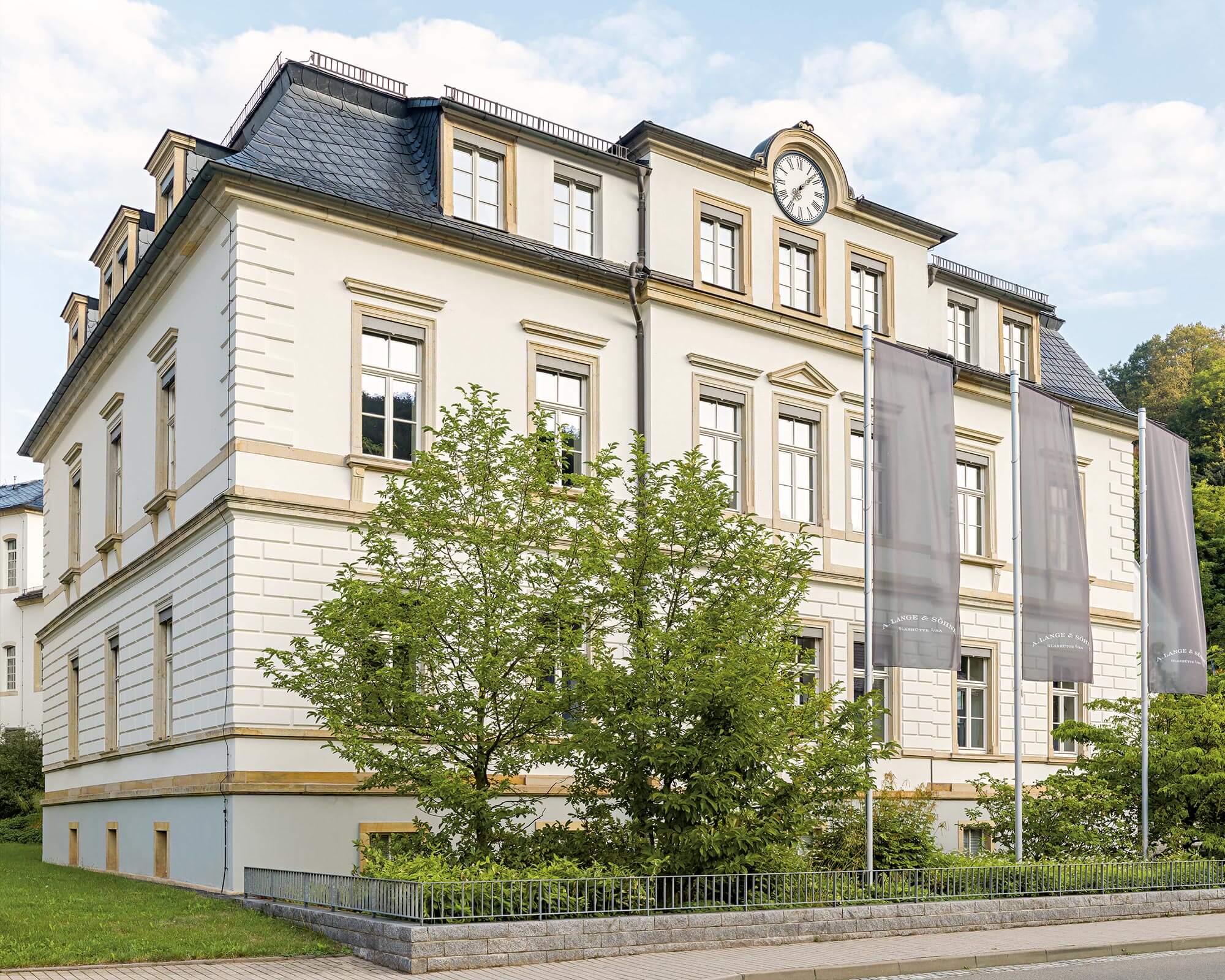
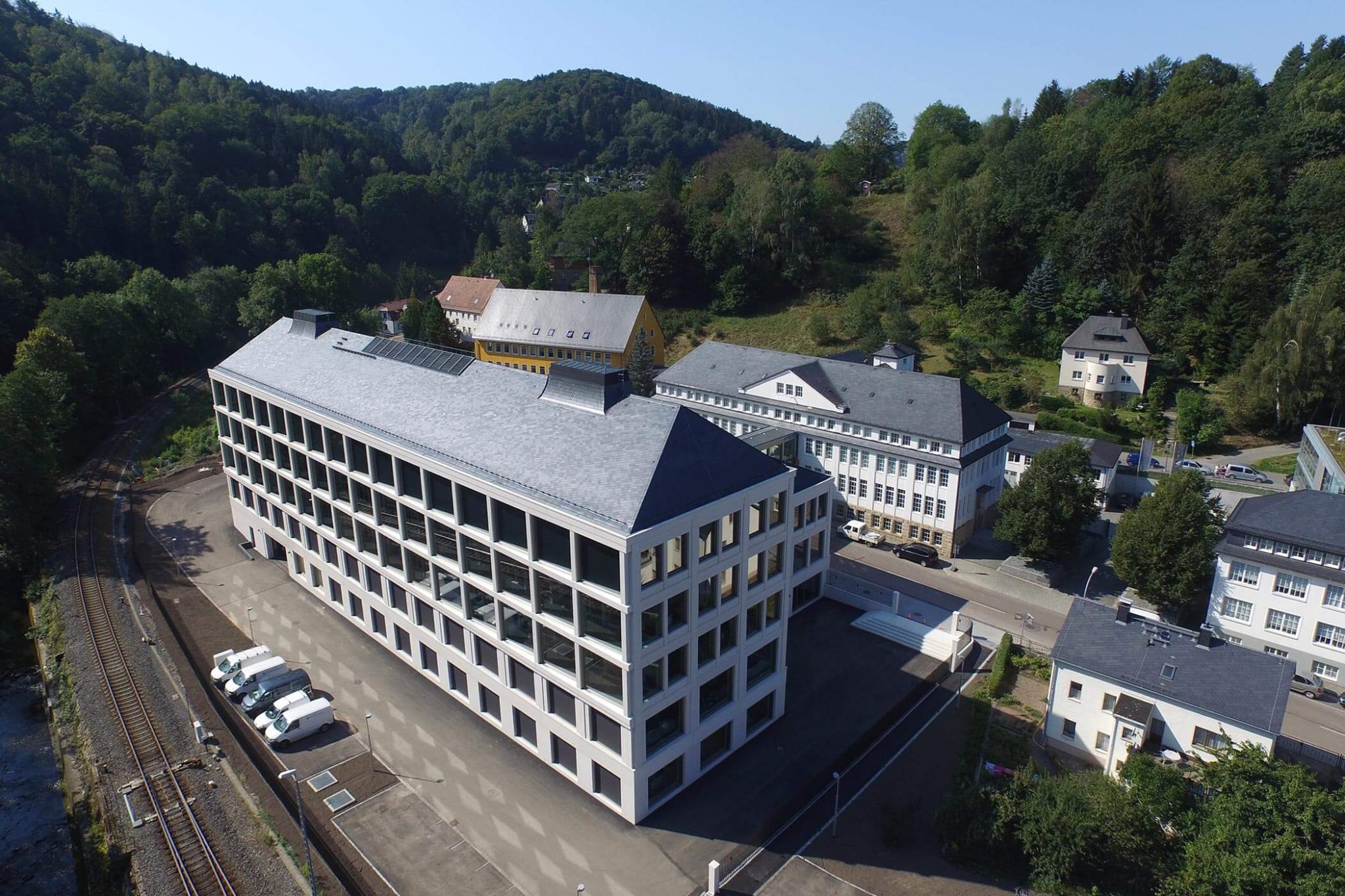
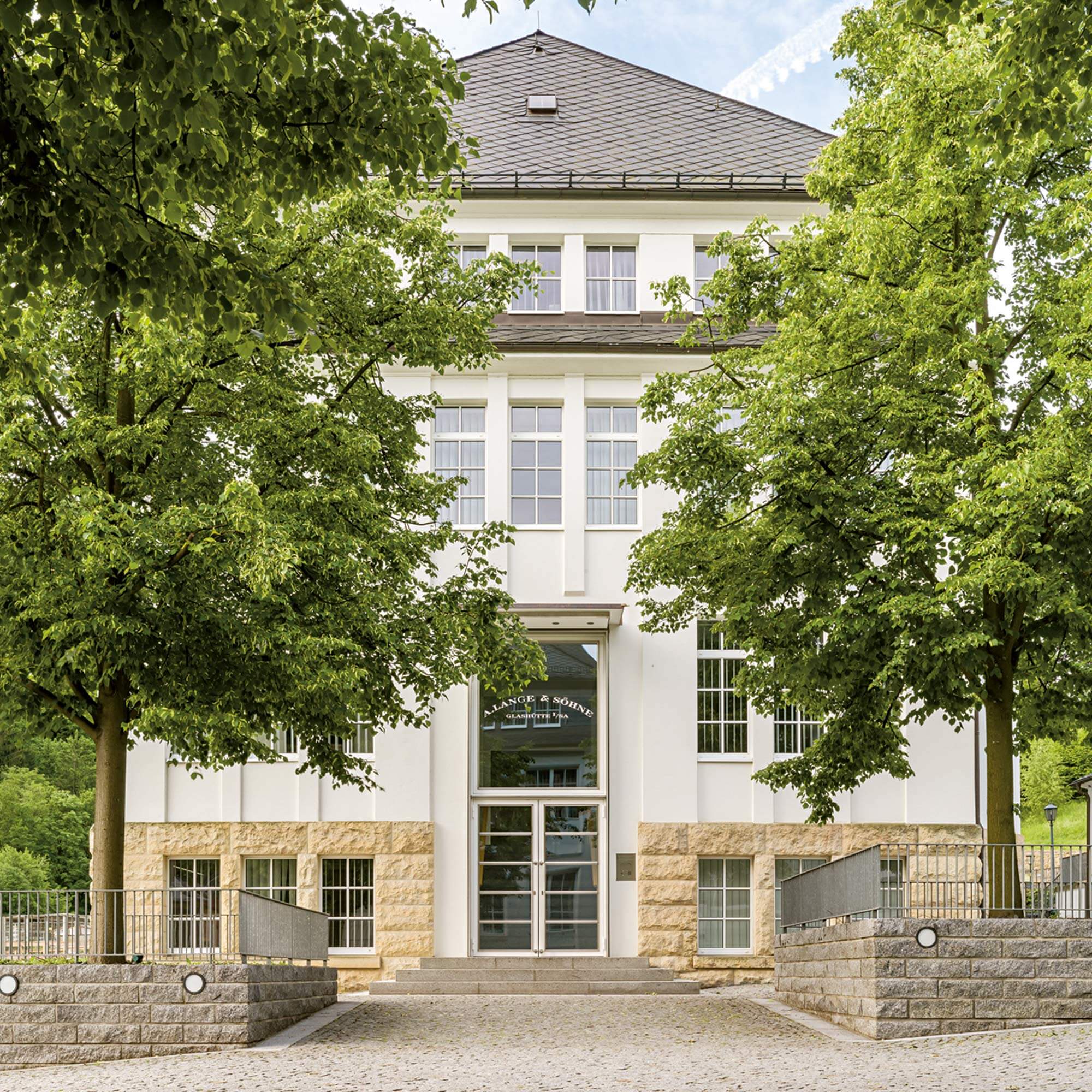
– Finishing
We first visit the artisans who are responsible for the many decorative techniques of the watch movements. The thing that never ceases to amaze us is the fact that there is no state-recognised training for this craft – everything here is done according to the mantra ‘learning by doing’. The finishers need around one to two years to master the many different techniques. It takes several months of practice just to be able to execute a flat polish to Lange’s standards. The great thing is that even talented individuals who have opted for a career change can learn the craft with the necessary discipline and passion. The components, almost all of which are finished by hand, are largely manufactured at the A. Lange & Söhne manufacture, and are predominantly made of nickel silver, steel, gold or brass.
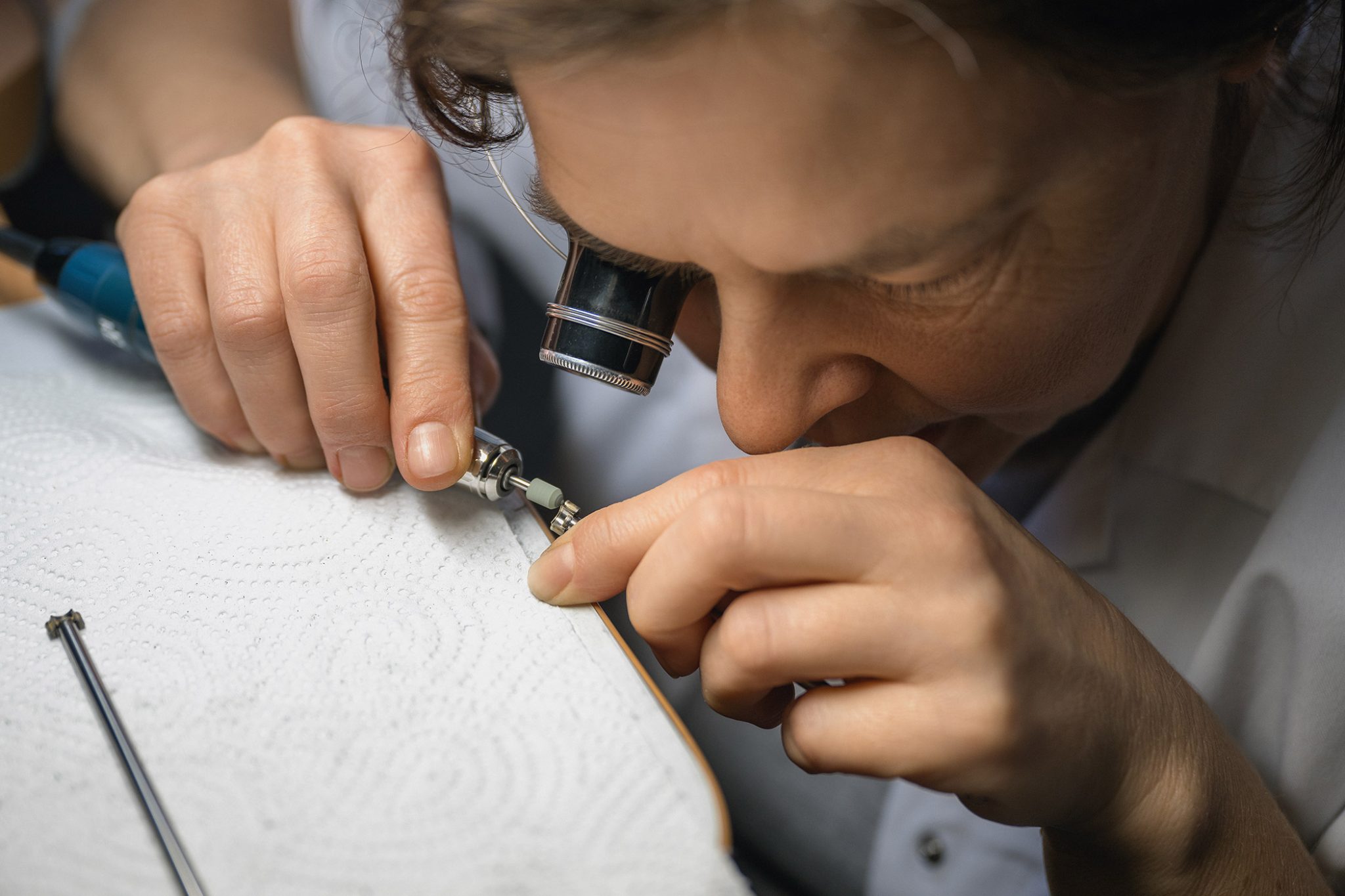
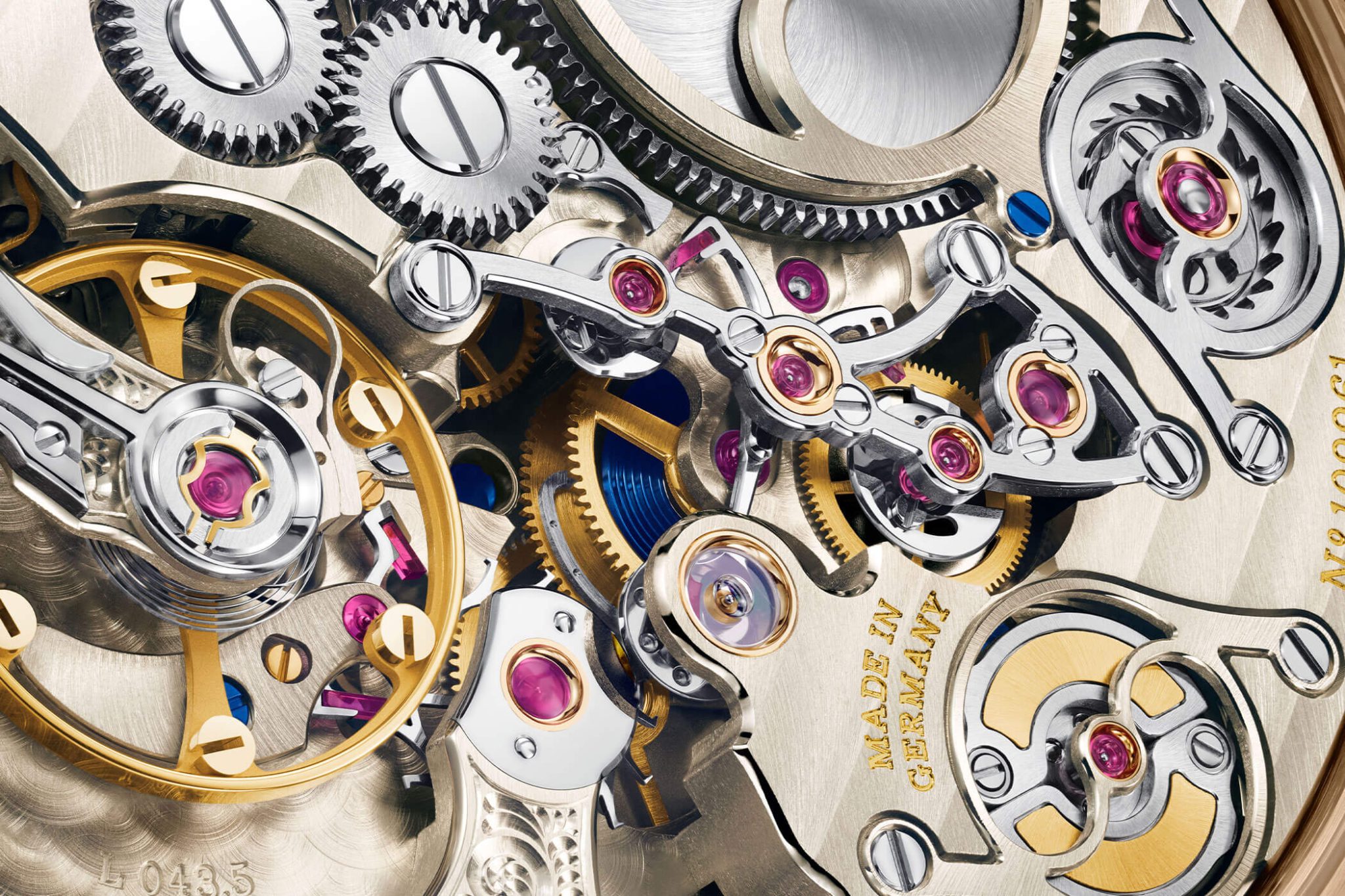
The engravers, however, need a little more practice. They all have to complete three years of training before they are allowed to immortalise their handwriting on Lange timepieces – and handwriting is to be understood literally, as the team of engravers can recognise which of them has decorated the balance cock just by looking at the lines on it. If a customer ever visits the manufacture, they can even have an autograph card signed by the engraver in question. There are currently only five engravers at Lange, so the responsible engraver is quickly identified. When talking to one of the young engravers, we learn that relief engraving is the most demanding decoration. The high art here is owed to the fact that the engraving appears raised and three-dimensional, and the engraver virtually carves the decoration out of the material.
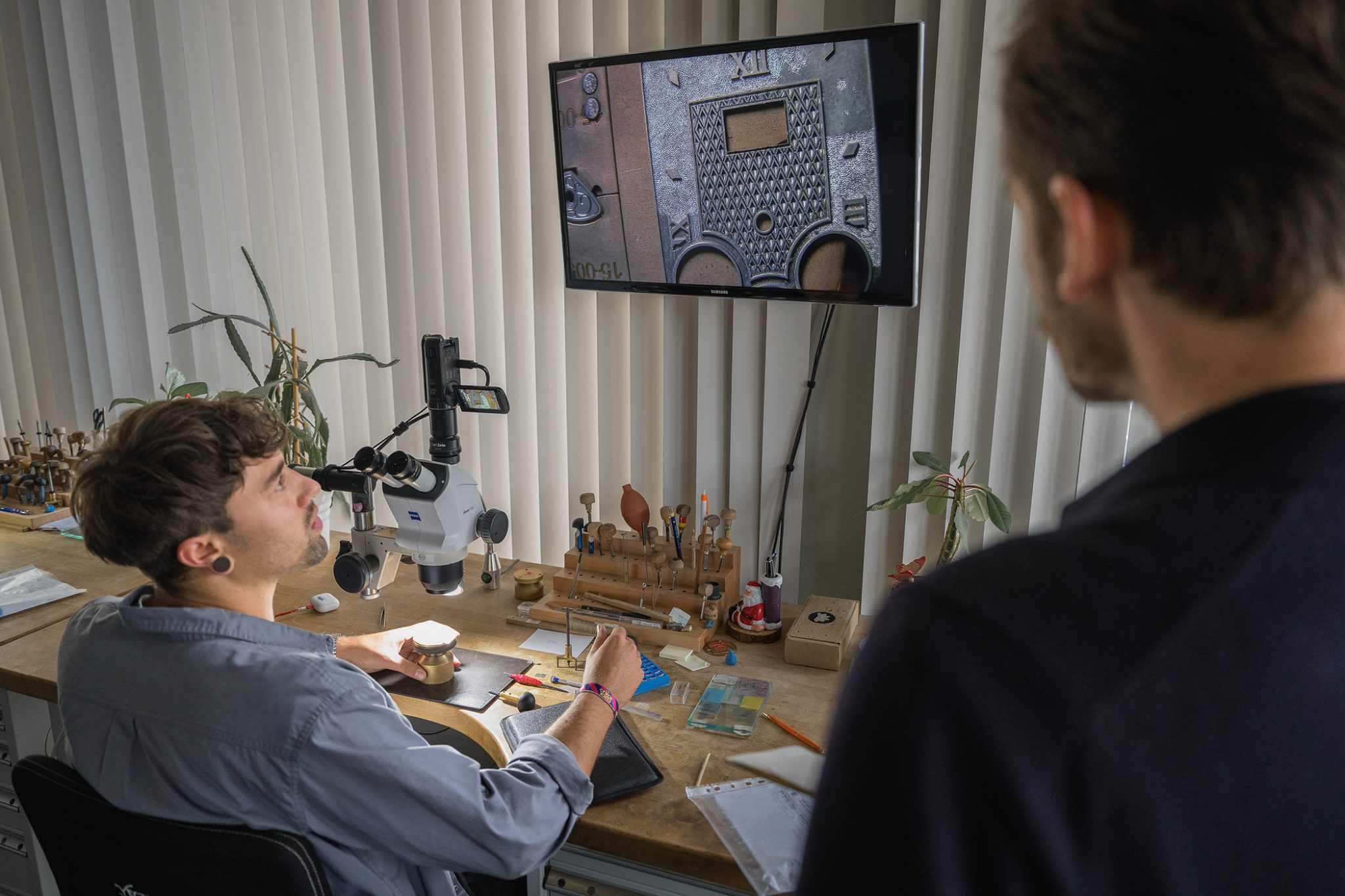
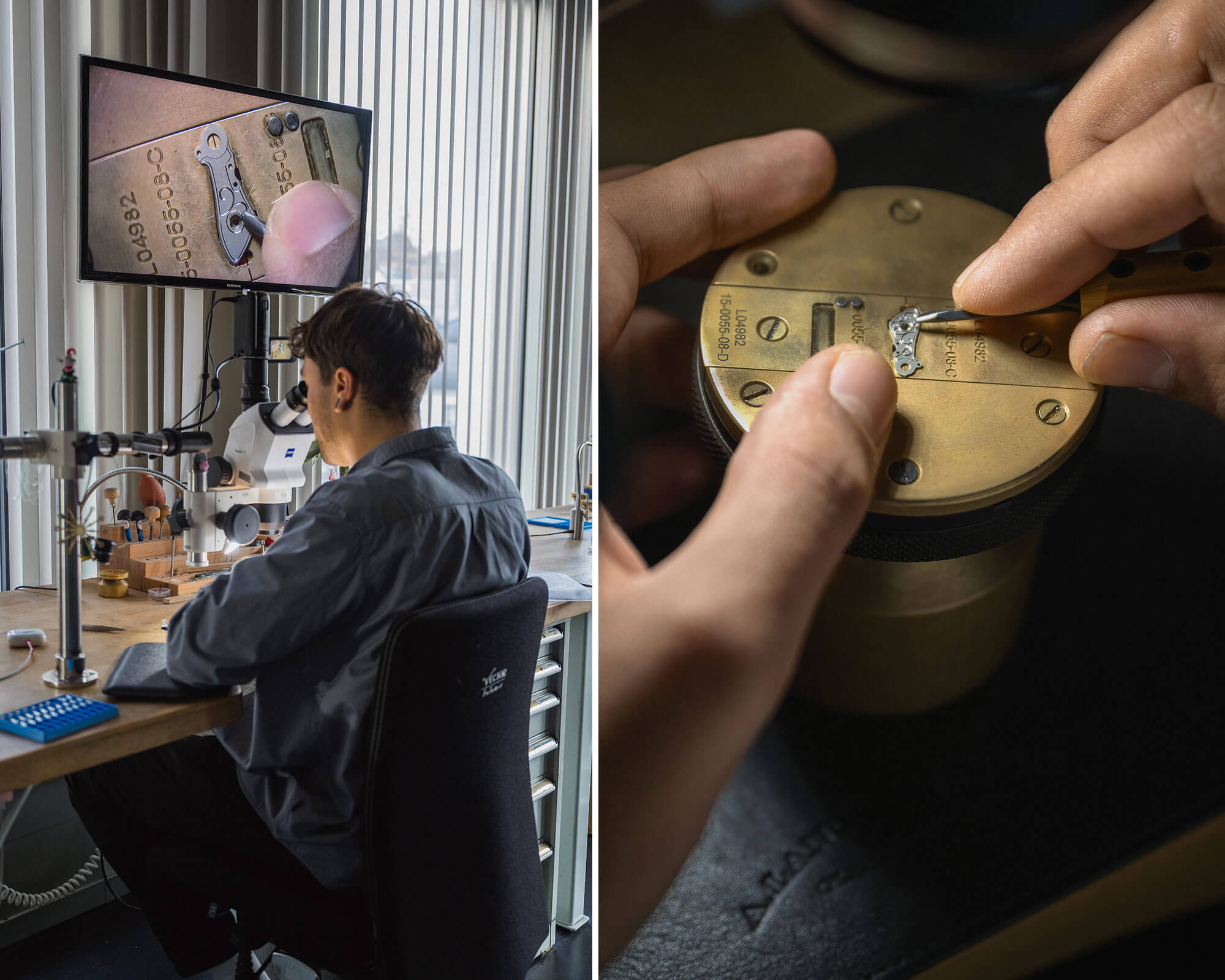
– Assembly
In this area of the manufacture, 17-20 employees work exclusively on the Lange 1. Even today, assembly is divided into departments, so that no one watchmaker is responsible for all steps, but rather each employee specialises in his or her activity in order to make the highest quality consistently reproducible. This is a manufacturing process that founder Ferdinand Adolph Lange already established by introducing the principle of division of labour.

What we experience here can only be understood if you visit the A. Lange & Söhne manufacture in person. At the many different tables, the watchmakers not only have the tiny components in front of them, but also precise instructions for each individual component, specifying the tolerance range in which they may be machined. We are standing in the micrometre range. Upon realising that a watch movement usually contains between 300 and over 1,000 components, we gain a completely different understanding of the effort that goes into producing a watch. There is even a separate lubrication plan for all moving parts.
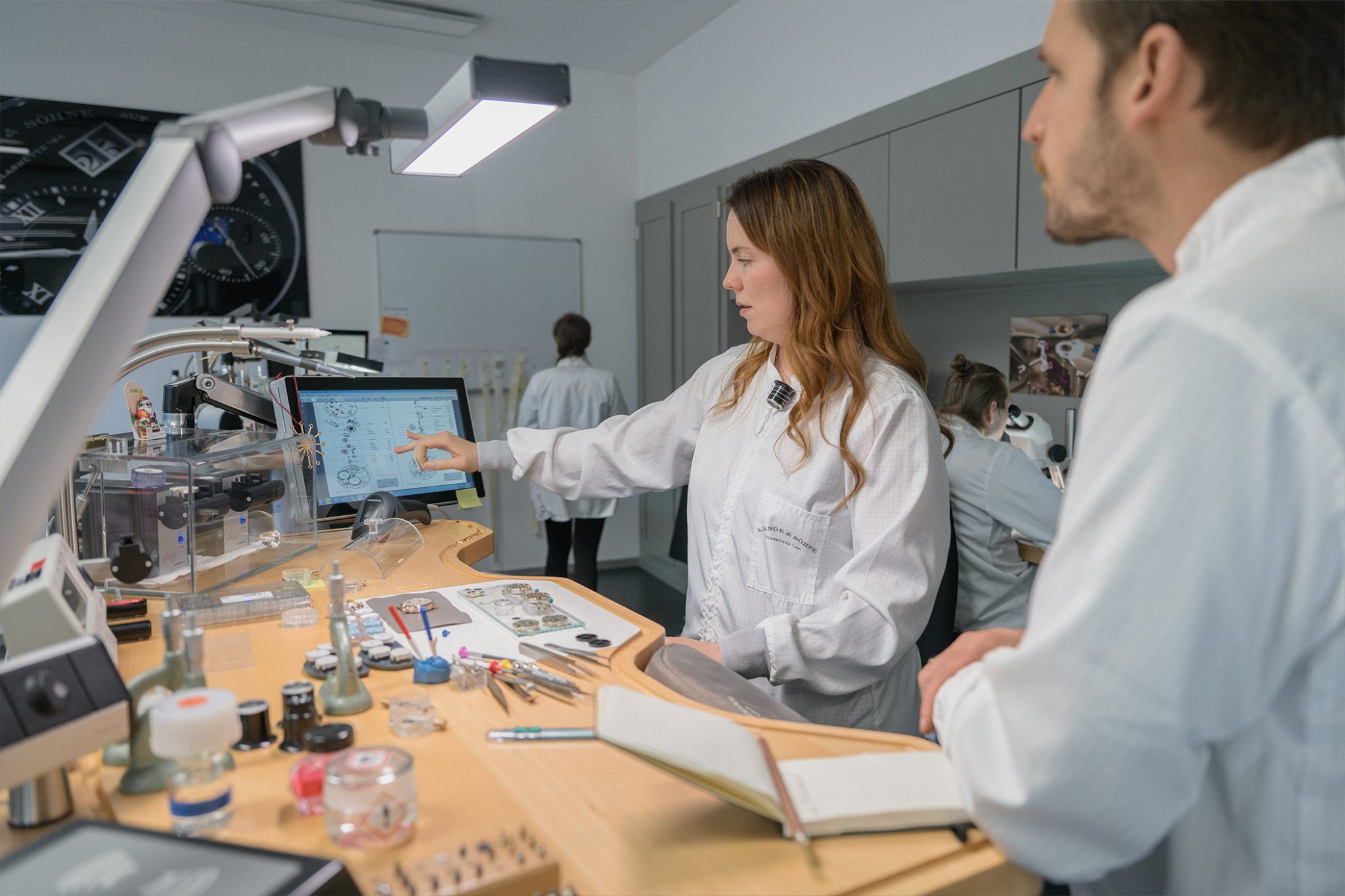
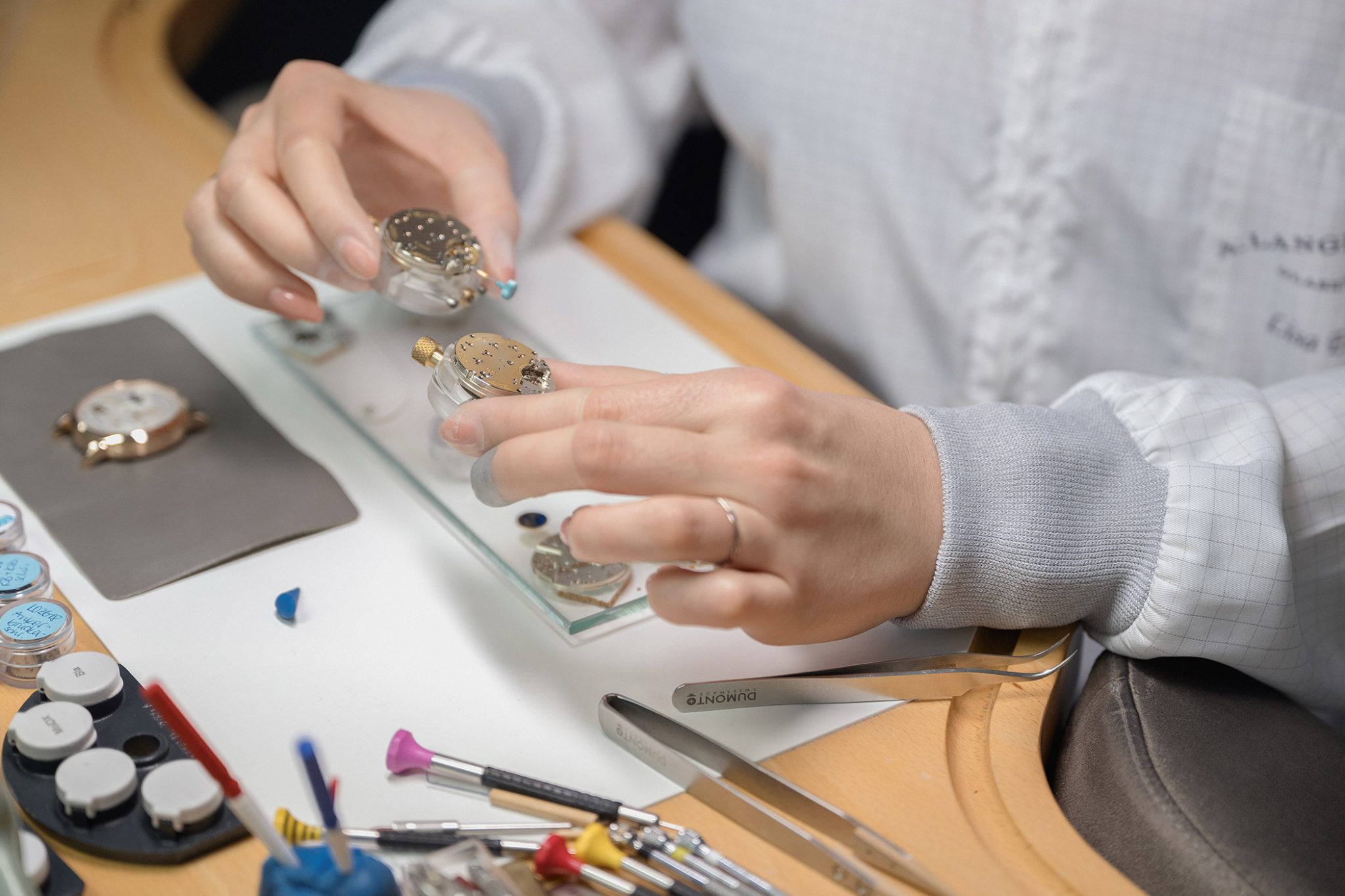
This is also where the secondary assembly takes place, as well as the two-week endurance test that all watches undergo once they have met all the assembly criteria. Watchmaking at this level is not left to chance – mistakes are not tolerated.

– Zeitwerk
20 people work in the department producing Lange’s Zeitwerk watches. The Zeitwerk was first presented in 2009 and was the first mechanical watch with an exact jumping digital time display, reminiscent of the legendary five-minute clock at the Semper Opera House. It has a jumping numerals mechanism consisting of three discs, which switches the three numerals in a fraction of a second. Of course, this requires an enormous amount of energy. The discs are 12 times heavier than conventional minute and second hands. In addition, it must be ensured that the movement is always driven with constant force in order to guarantee rate stability. This is because the tension spring torque decreases over time. Accordingly, Lange and its chief developer Anthony de Haas developed a patented re-tensioning mechanism (remontoir). This mechanism ensures a constant torque over the entire running time and acts as a pulse generator for the jumping numeral mechanism. The intermediate mainspring of the remontoir stores energy for one minute before receiving new energy from the large double mainspring barrel. A specially developed wind trap absorbs excess energy through the air resistance created by its rotation. Both components are no bigger than your little fingernail, but are nevertheless extremely effective.
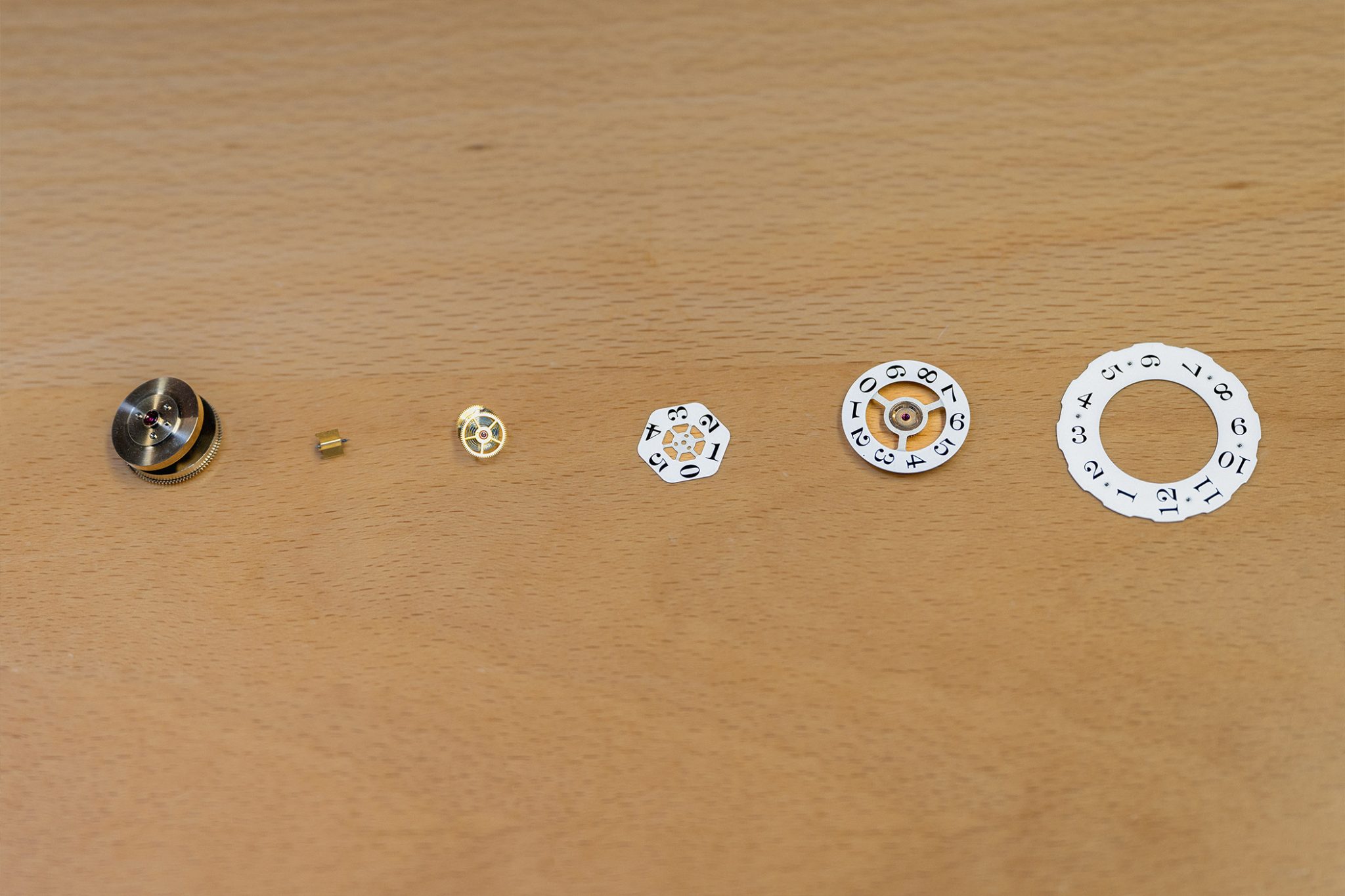
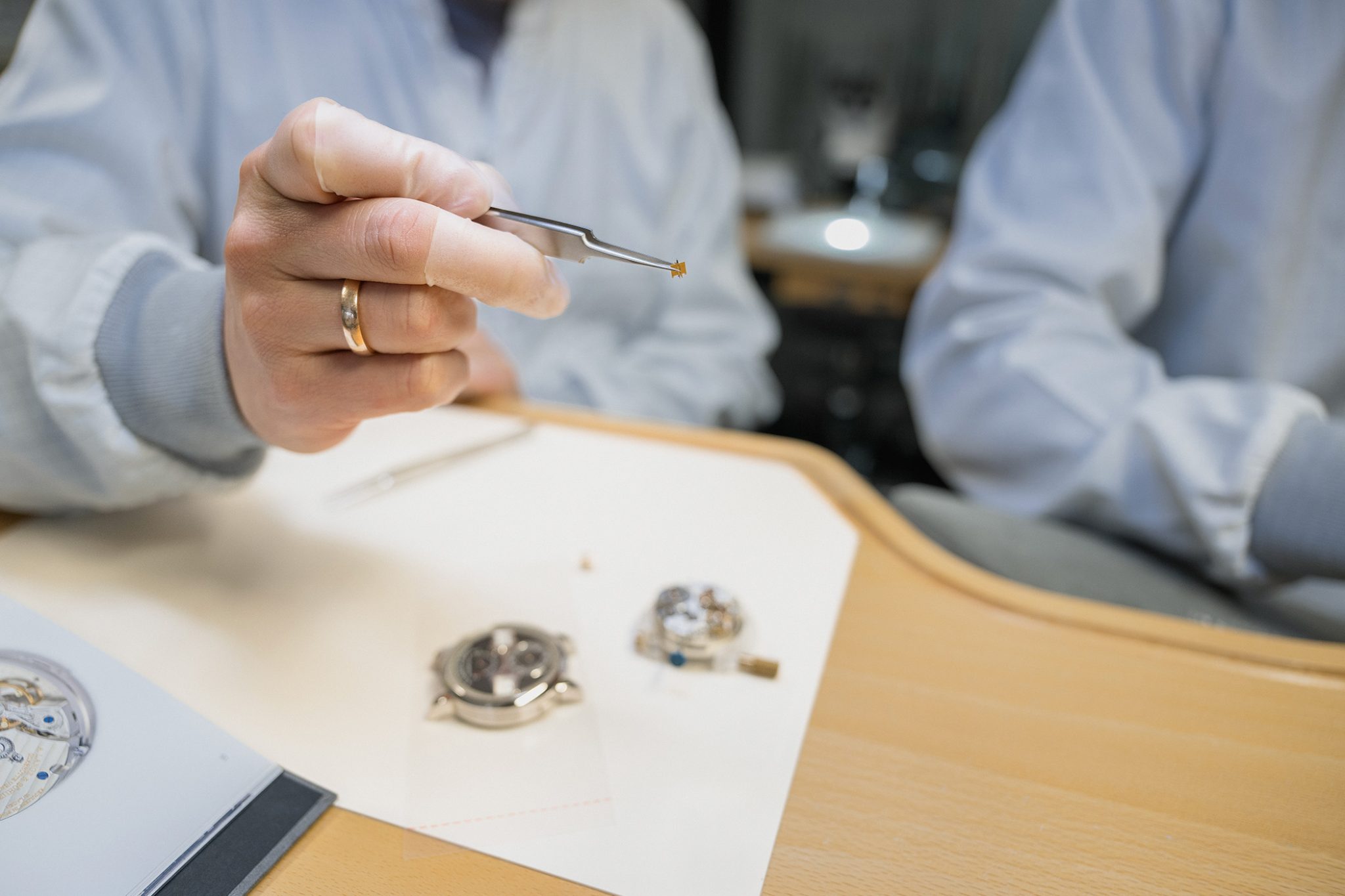
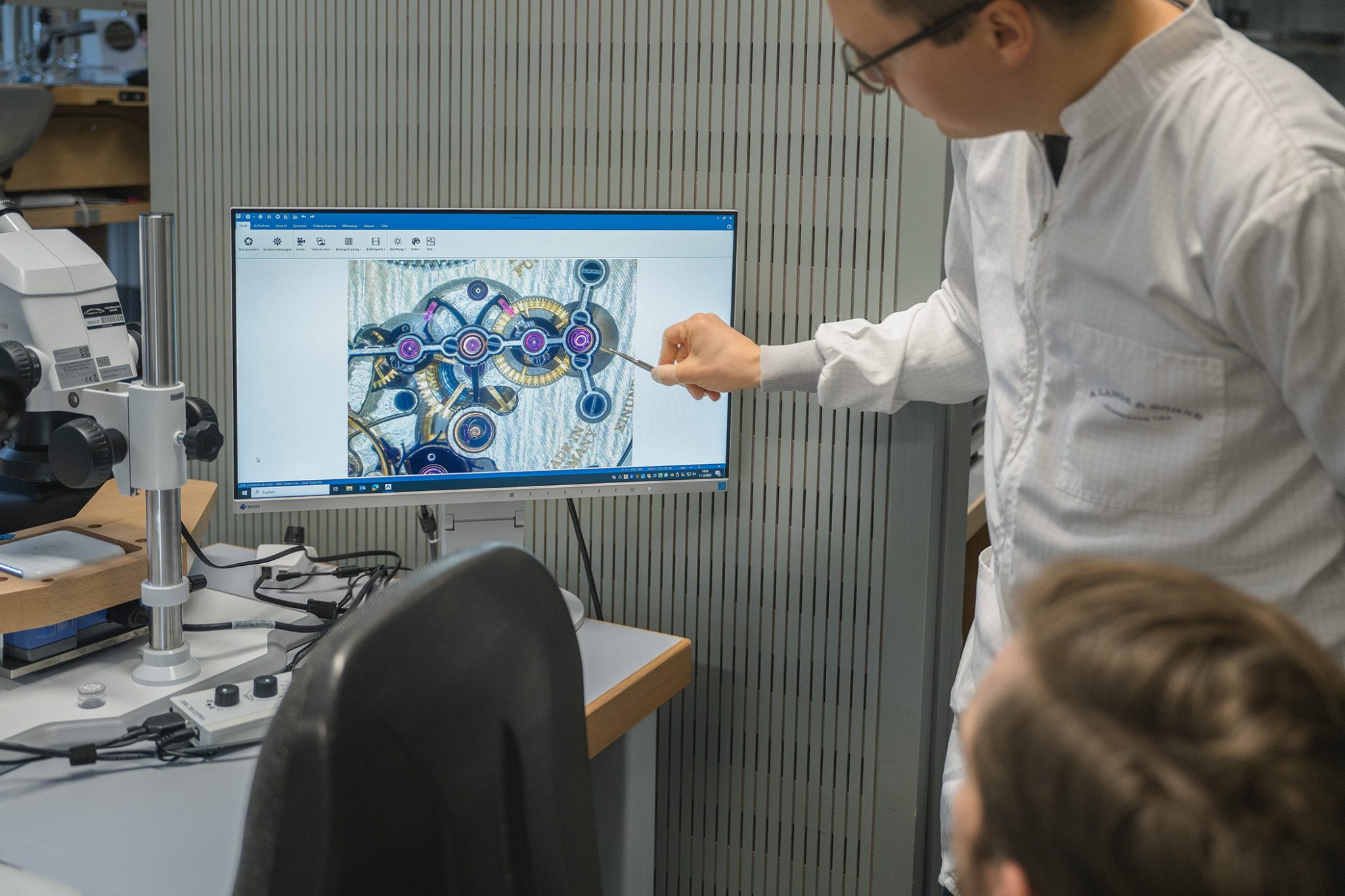

But that’s not all – the power reserve of the first generation of Zeitwerk was 36 hours (calibre L043.1). In 2022, the team around de Haas presented the new calibre L043.6, offering double the power reserve at 72 hours. Furthermore, despite the increase in performance, the movement is even thinner than its 9.3 mm predecessor, with a height of 8.9 mm.
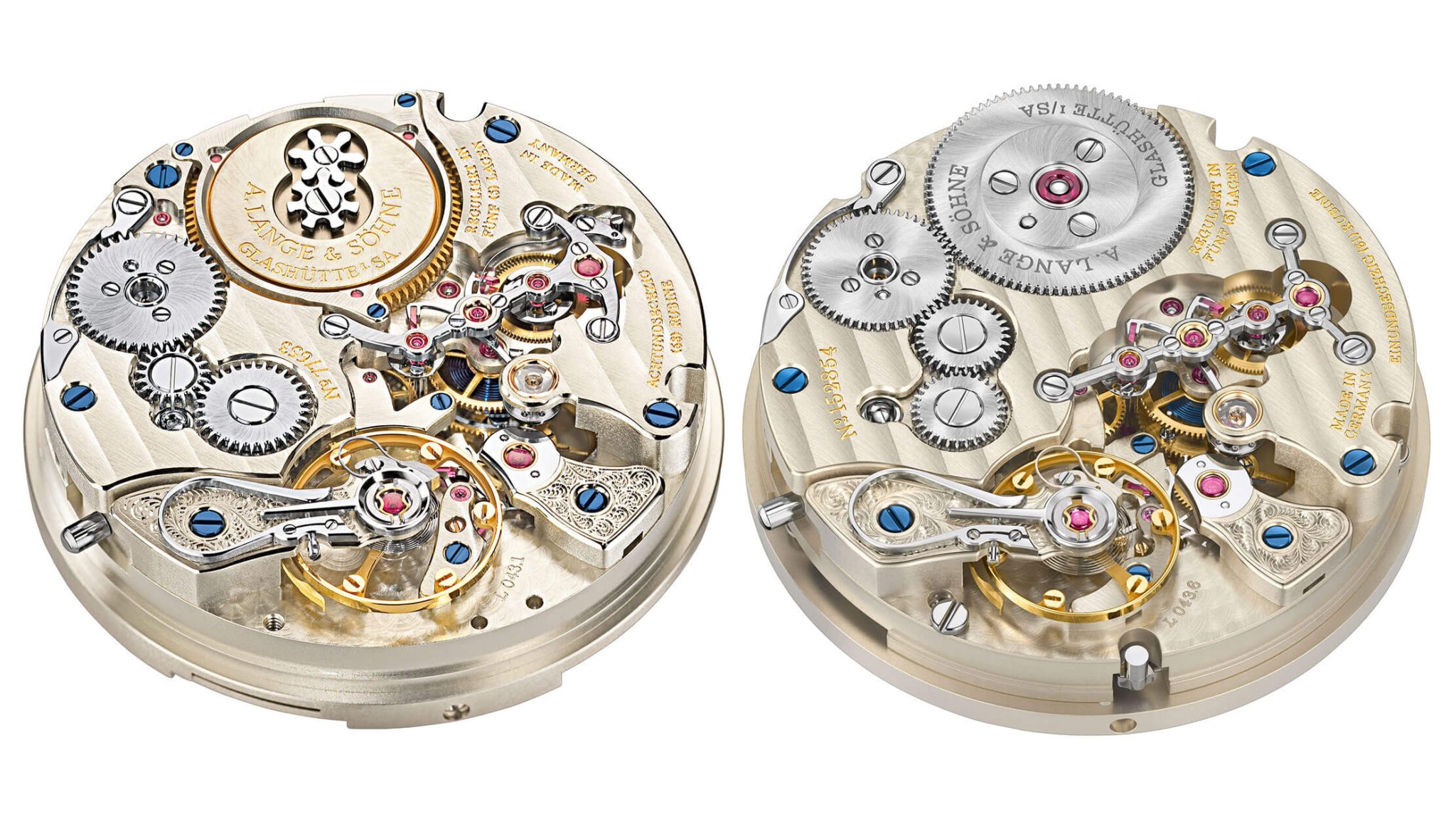
Kaliber L043.1 (links) und Kaliber L043.6 (rechts)
– Complication department
We take a quick look at the department for the company’s biggest complications, even though development takes place in a separate department. This is where the likes of the Tourbograph are assembled. We talk to another young watchmaker, encountering some difficulty following the shop talk about the greatest technical challenges of Lange’s most complicated watches. What we do undoubtedly pick up on from the watchmaker is, at the very least, a deep admiration and great respect for the enormous depth of knowledge already amassed, as well as a desire to do even better and find new technical solutions. 12 employees work here on tourbillons, perpetual calendars and minute repeaters. According to the watchmaker, the tourbillon with its five complications is one of Lange’s most complicated models. In addition to the tourbillon, chronograph rattrapante and perpetual calendar, it also has a traditional chain and fusée drive. One such tiny chain is lying in front of us and we learn that it consists of over 600 parts and can carry a weight of two kilos.
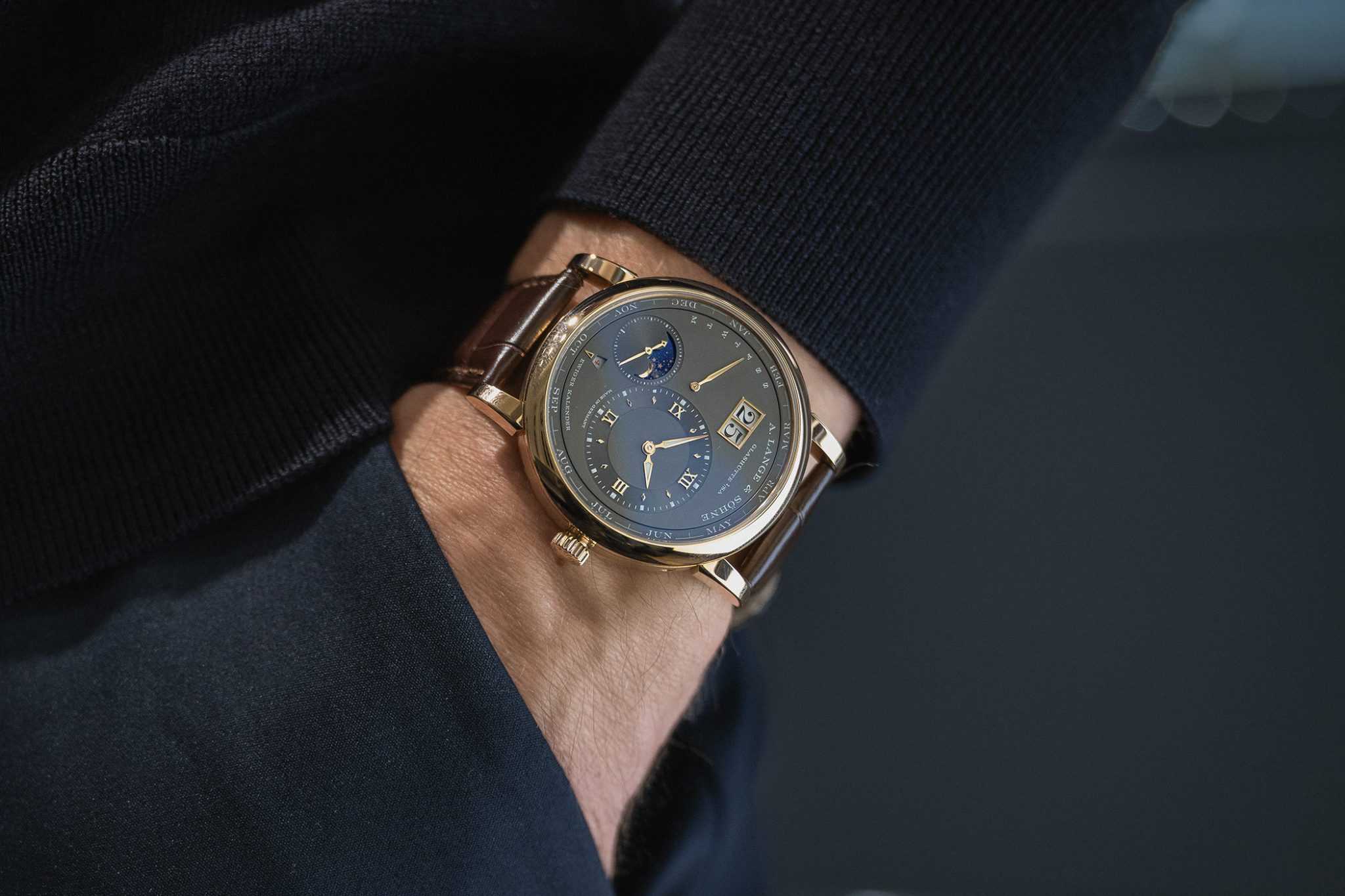
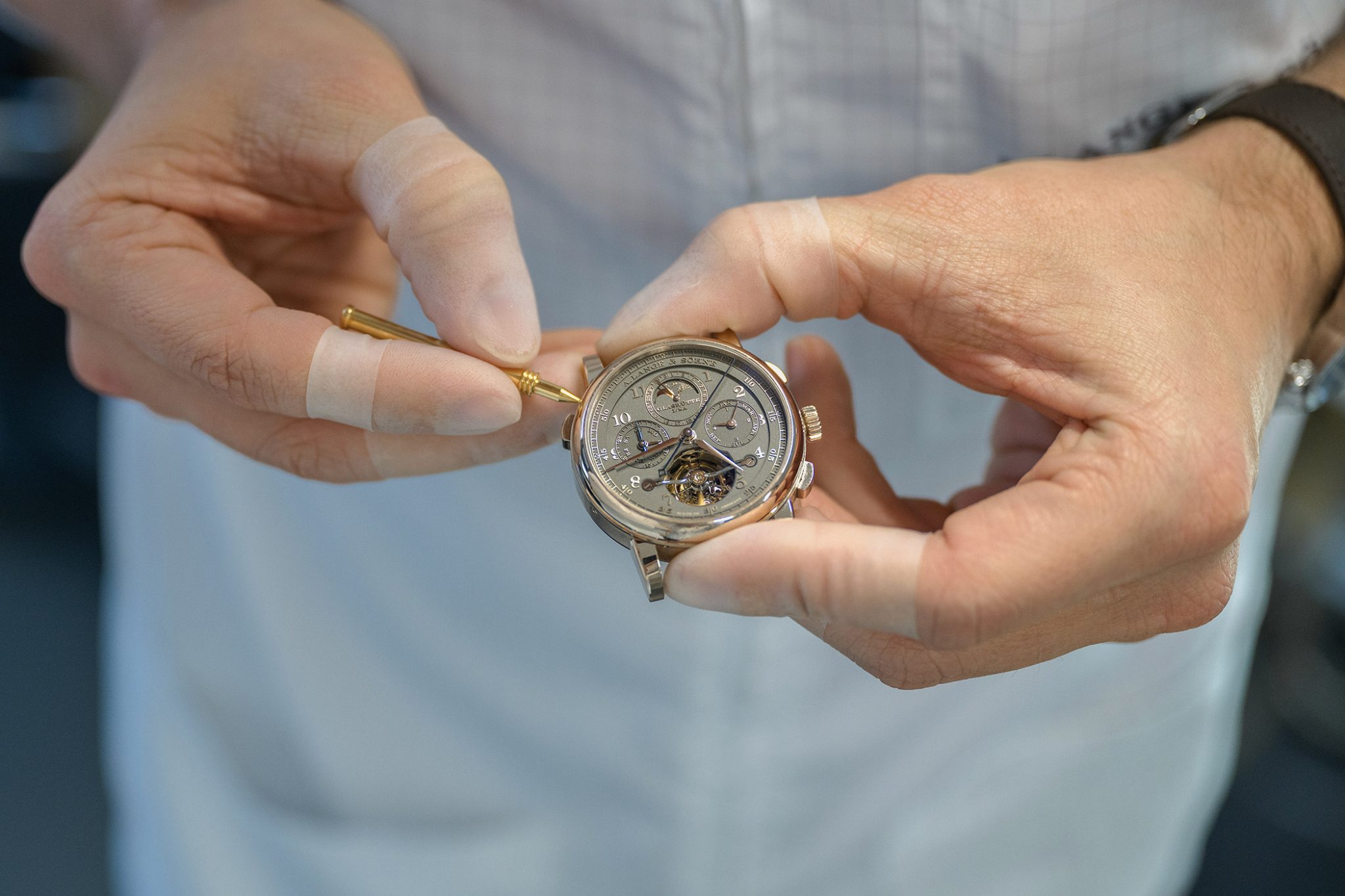
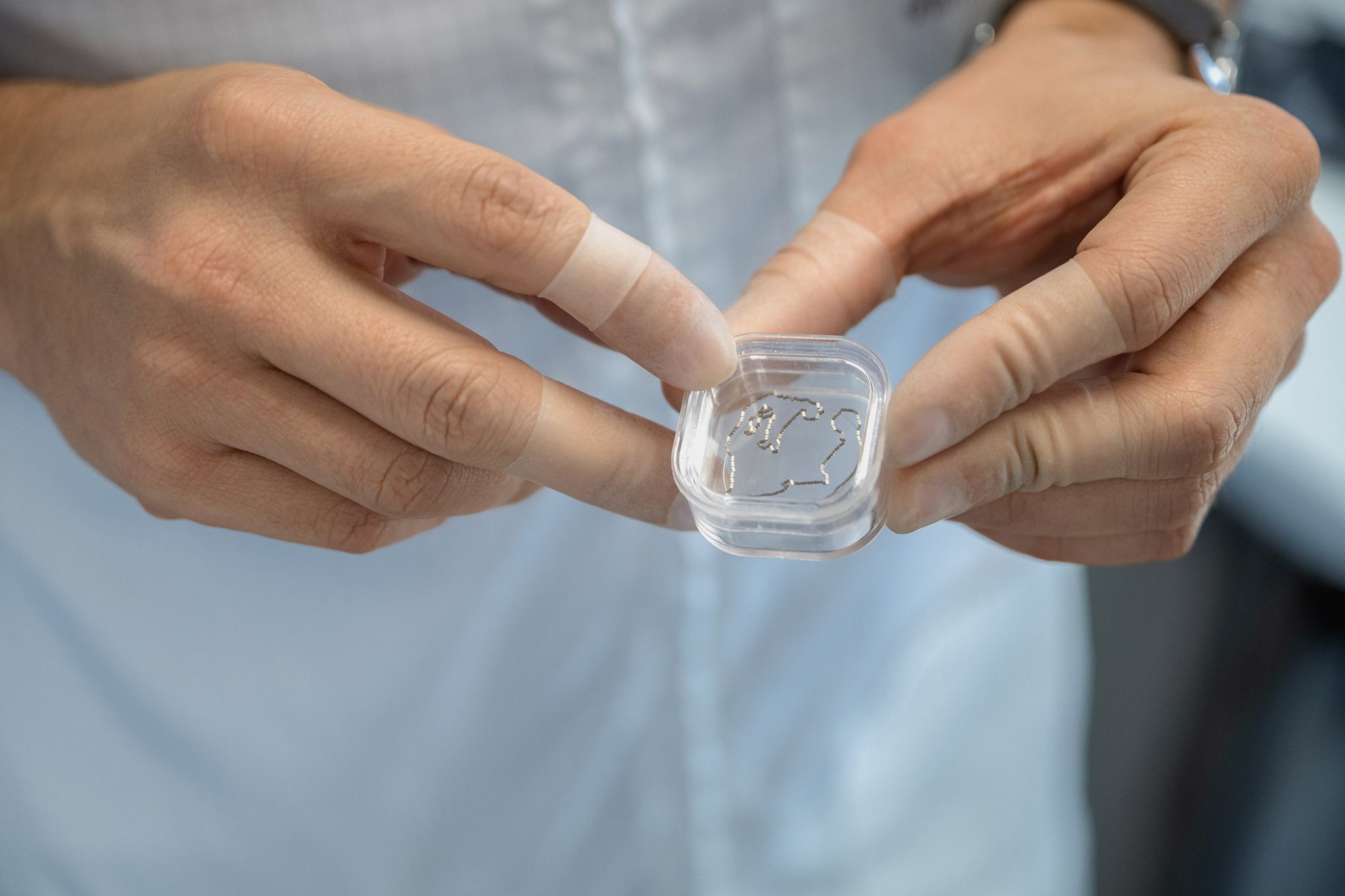
Last but not least, we meet Anthony de Haas, who has been responsible for the development of these highly sophisticated movements for 20 years. He tells us about his early years at Lange and a formative event when he sat down with his watchmakers and posed the question of designing a watch with a power reserve of one month. The idea was so crazy for his technicians that they didn’t even consider it. De Haas responded, “If you can tell me in three weeks why it’s impossible, then we won’t do it”. After a few weeks, they met again and his designers presented him with the first technical designs. In 2007, A. Lange & Söhne then presented the Lange 31, the world’s first mechanical wristwatch with a power reserve of 31 days. De Haas and his team had developed a patented rewinding mechanism to gently and evenly transfer the enormous energy of the two 1850-millimetre-long mainsprings to the movement.
Anthony de Haas, Director Product Development
As Walter Lange once said, “There is something you should expect not only from a watch, but also from yourself: Never stand still”. Today, the watchmaking company still aspires to not only build the best watches, but also to constantly develop and explore their technical boundaries, even pushing them at times. Here at the manufacture, A. Lange & Söhne live a life that never stands still.
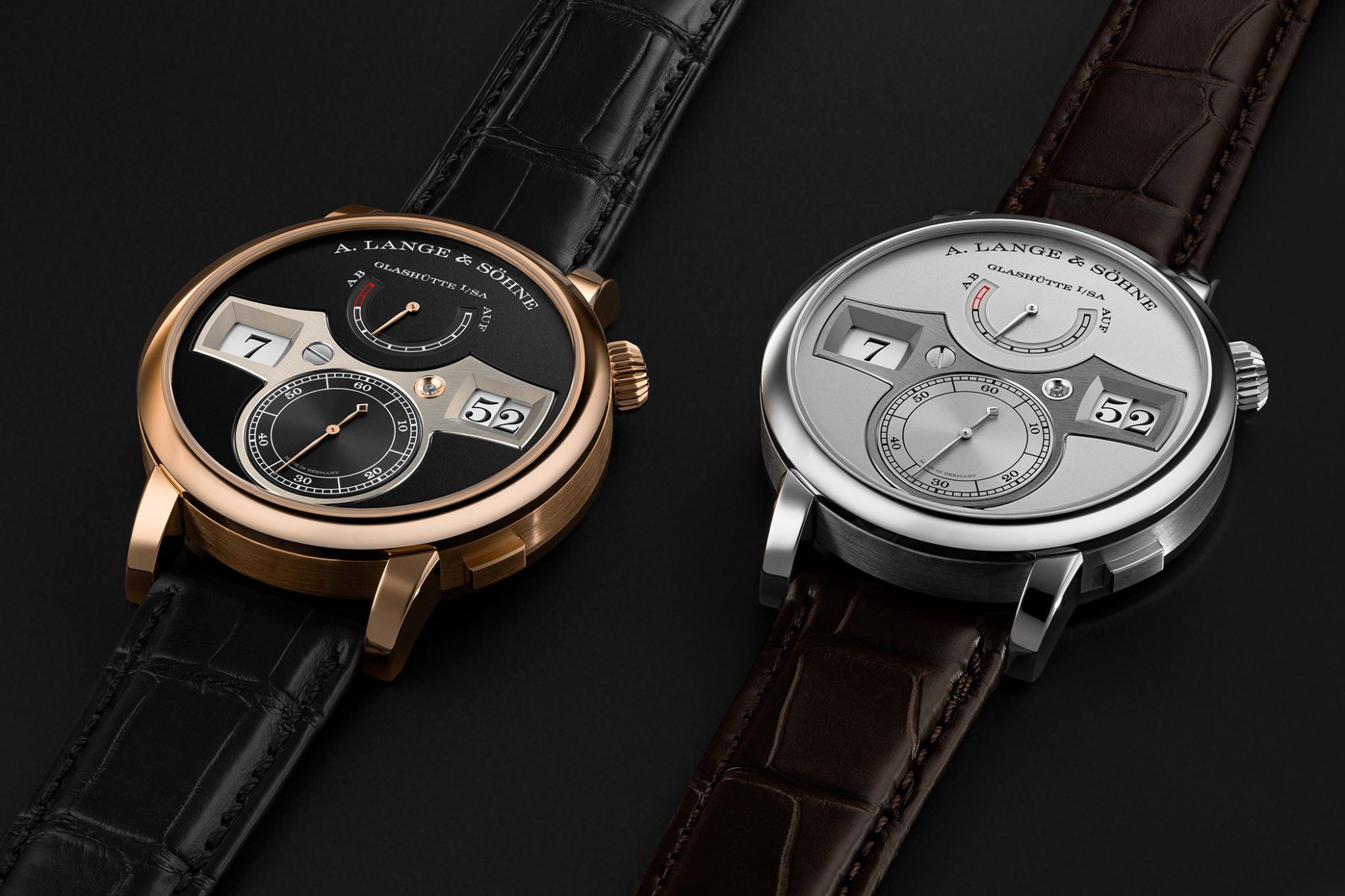
A. Lange & Söhne Zeitwerk