Back in January at Dubai's LVMH 2020 watch fair, watch manufacturer Zenith introduced several new models created in cooperation with a number of acknowledged artists and brands. One model was developed in partnership with British automotive manufacturer Land Rover and pays homage to its Defender: the new DEFY 21 Land Rover Edition. At the same…
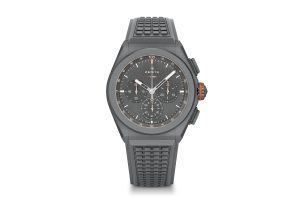